Unveiling the Intricacies of Bulk Steel in Modern Manufacturing
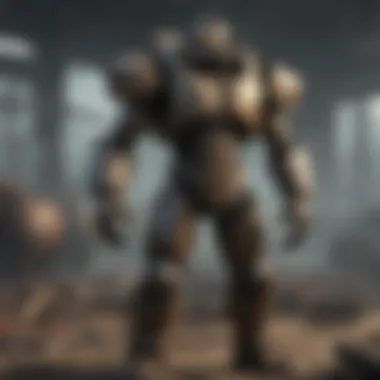
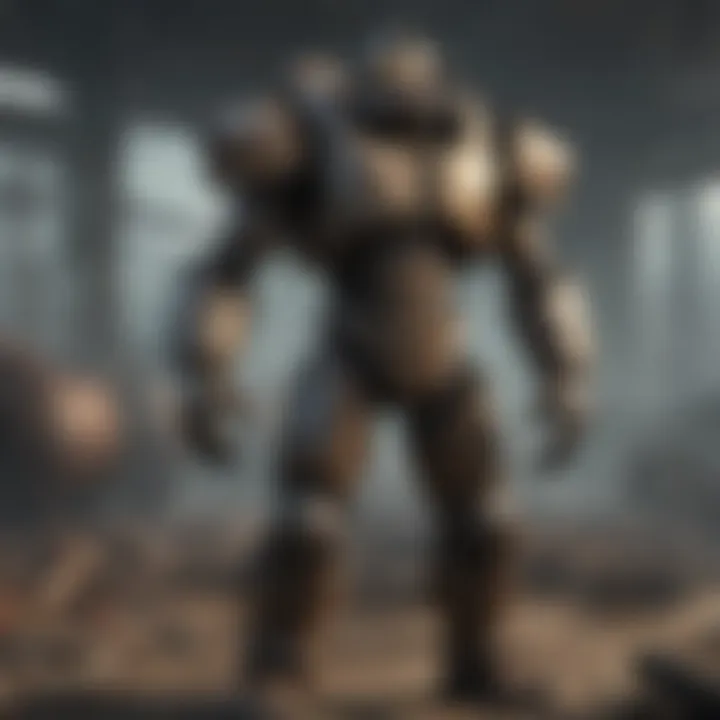
Lore Insights
Bulk steel in manufacturing processes holds a pivotal role akin to the foundation of a sturdy structure. To grasp the essence of bulk steel, one must first unravel its origins and evolution in the realm of metallurgy. From the early discoveries of crude iron to the intricate alloying techniques of modern times, the journey of bulk steel parallels the progress of humanity itself.
In examining the applications of bulk steel, a diverse tapestry unfolds before us, showcasing its presence in multifaceted industries. Whether fortifying towering skyscrapers, constructing intricate machinery, or shaping resilient infrastructure, bulk steel stands as a testament to human ingenuity and innovation.
Gameplay Tips and Strategies
For the uninitiated, navigating the intricate landscape of bulk steel can be as daunting as embarking on a new quest in the Fallout universe. Just as vault dwellers must equip themselves with the right tools for survival, manufacturers and industrialists must heed essential guidelines when working with bulk steel.
Delving deeper, a careful selection of equipment and resources can significantly impact the efficiency and quality of bulk steel production. Much like scavenging for rare components in a post-apocalyptic wasteland, optimizing resources and honing techniques are paramount for achieving optimal results when working with this versatile material.
Character Analysis
Within the intricate web of manufacturing and metallurgy, bulk steel emerges as a central character, embodying strength, versatility, and resilience. As we delve into the profiles of iconic steel alloys and compositions, each reveals a unique persona with distinct attributes and applications.
Moreover, exploring the relationships between different types of bulk steel sheds light on the interconnectedness of industrial processes and material science. Similar to the intricate dynamics between characters in a thrilling narrative, the synergy between various steel components shapes the outcome of manufacturing endeavors.
News and Updates
Stay informed about the latest advancements and innovations in bulk steel manufacturing with our comprehensive coverage of industry updates. From breakthrough techniques in steel production to upcoming trends in metallurgical engineering, our curated news section brings you the latest developments straight from the furnace of progress.
Keep abreast of patch notes, DLC releases, and community events that shape the ongoing narrative of bulk steel in manufacturing. As developers continue to refine the gameplay of steel production, our news segment offers a glimpse into the evolving landscape of industrial practices and technological advancements.
Fan Theories and Speculations
Venture into the realm of speculative discourse as we explore popular theories and unresolved mysteries surrounding the world of bulk steel in manufacturing. From enigmatic production processes to the potential for future innovations, our speculation corner dives deep into the intricacies of metallurgical conjecture.
Engage in discussions on emerging trends, unresolved plot points, and potential revelations that could shape the future of bulk steel applications. As we peer through the lens of speculation, the landscape of bulk steel manufacturing unveils a tapestry of possibilities and conjectures waiting to be explored.
Introduction to Bulk Steel
Bulk steel plays a pivotal role in various industries, proving to be a cornerstone of modern manufacturing processes. Understanding the significance of bulk steel is crucial for enthusiasts of metallurgy and industrial practices. Exploring the characteristics and applications of bulk steel provides valuable insights into its utilization across different sectors.
Definition and Characteristics
Composition of Bulk Steel
Bulk steel is primarily composed of iron with varying amounts of carbon and other elements like manganese, nickel, and chromium. This composition contributes to the strength and durability of bulk steel, making it a preferred choice for structural applications in construction and automotive industries. The unique blend of elements in bulk steel enhances its mechanical properties, providing excellent tensile strength and impact resistance.
Physical Properties
Bulk steel exhibits exceptional physical properties such as high hardness, toughness, and ductility. These properties make bulk steel suitable for a wide range of manufacturing processes like machining and fabrication. The physical robustness of steel enables it to withstand harsh environmental conditions and heavy loads, ensuring longevity and reliability in diverse applications.
Chemical Properties
The chemical properties of bulk steel determine its corrosion resistance and weldability. By alloying steel with elements like chromium and nickel, stainless steel is created, offering excellent resistance to rust and oxidation. Understanding the chemical composition of steel aids in selecting the right type for specific applications, ensuring optimal performance and longevity.
Types of Bulk Steel
Carbon Steel
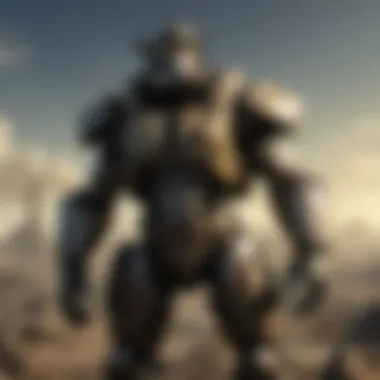
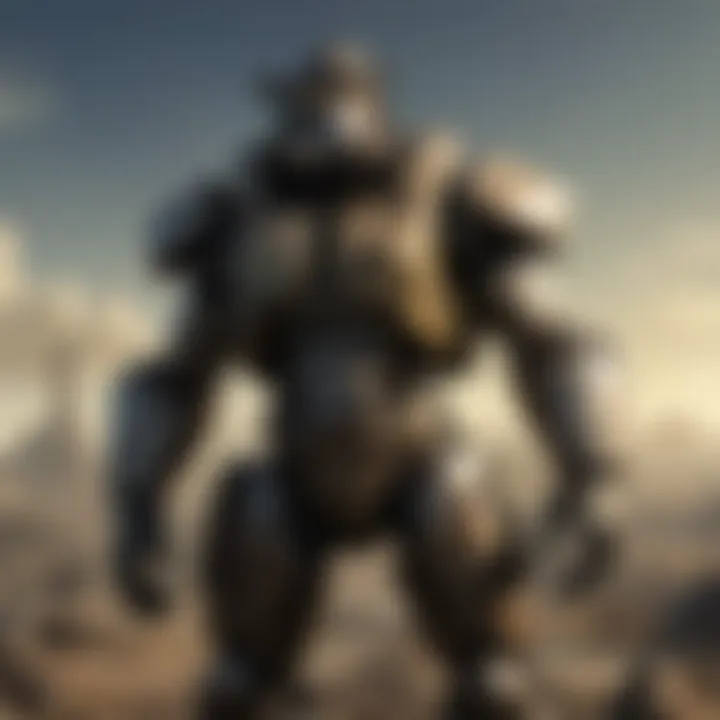
Carbon steel is a popular choice in manufacturing due to its high tensile strength and affordability. With varying carbon content, carbon steel can be tailored to specific requirements, making it versatile for different applications. The versatility and ease of modification of carbon steel make it a preferred material for producing a wide range of products.
Alloy Steel
Alloy steel blends iron with other elements like manganese, silicon, and copper to enhance specific properties. The addition of alloying elements imparts superior strength, hardness, and wear resistance to steel, making it suitable for specialized applications in industries like aerospace and automotive.
Stainless Steel
Stainless steel is renowned for its corrosion resistance and hygiene properties, making it ideal for food processing and medical equipment. The alloying of chromium and nickel in stainless steel provides an attractive finish and exceptional durability, ensuring long-term performance in challenging environments.
Production Methods
Blast Furnace Process
The blast furnace process involves the smelting of iron ore with coke and limestone to produce molten iron. This method is cost-effective and enables large-scale production of raw steel, making it a fundamental process in the steel industry. The blast furnace process is energy-intensive but crucial for supplying molten iron to various downstream manufacturing operations.
Electric Arc Furnace Process
In the electric arc furnace process, recycled steel scrap is melted down using an electric arc to create new steel. This method is environmentally friendly as it minimizes raw material usage and energy consumption. The electric arc furnace process is flexible and efficient, allowing for precise control over steel composition and quality.
Basic Oxygen Furnace Process
The basic oxygen furnace process involves blowing oxygen through molten iron to remove impurities and refine the steel composition. This method is efficient in producing high-quality steel with low levels of impurities. The basic oxygen furnace process is widely used for manufacturing structural steel and sheet metal, meeting stringent quality standards.
Applications of Bulk Steel
In the realm of manufacturing, the applications of bulk steel play a pivotal role in various industries. The use of bulk steel in manufacturing processes is integral to producing high-quality goods. Its significance lies in the impeccable strength, durability, and versatility it offers across different applications. Bulk steel is a cornerstone material in the engineering world, particularly in the automotive industry, construction sector, and diverse manufacturing processes.
Automotive Industry
Vehicle Manufacturing
Vehicle manufacturing stands as a significant sector where bulk steel finds extensive application. The process of vehicle manufacturing relies heavily on the strength and durability of materials used, making bulk steel an optimal choice. Its high tensile strength ensures the structural integrity of vehicles, providing safety and reliability. Utilizing bulk steel in vehicle manufacturing contributes to the industry's ability to create robust and long-lasting automobiles.
Structural Components
In the automotive industry, structural components are vital for the overall performance and safety of vehicles. Bulk steel is favored for structural components due to its superior properties, such as shock absorption and crash resistance. The unique feature of bulk steel lies in its ability to withstand intense impacts, enhancing the safety of vehicle occupants. While bulk steel excels in providing structural stability, its weight can sometimes be a disadvantage, impacting fuel efficiency.
Construction Sector
Building Structures
Building structures heavily rely on the durability and strength of materials, making bulk steel a prime choice. The key characteristic that makes bulk steel ideal for building structures is its robust nature, ensuring the integrity of constructions. Bulk steel's unique feature lies in its ability to support heavy loads and resist external forces, making it indispensable in constructing skyscrapers and large infrastructures. However, the downside may be its susceptibility to corrosion if not adequately maintained.
Infrastructure Development
In the construction sector, infrastructure development is a crucial application of bulk steel. The key characteristic of bulk steel in infrastructure lies in its longevity and reliability, ensuring the longevity of structures. Bulk steel plays a vital role in developing bridges, highways, and other essential infrastructure, providing stability and support. Despite its advantages, bulk steel may pose challenges in terms of specialized equipment requirements and skilled labor needs.
Manufacturing Processes
Machining
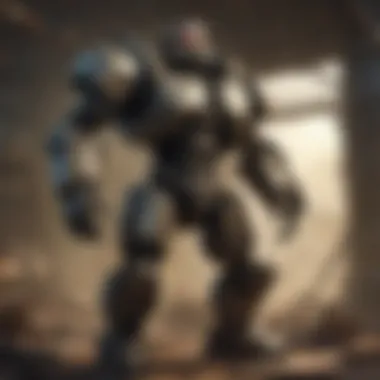
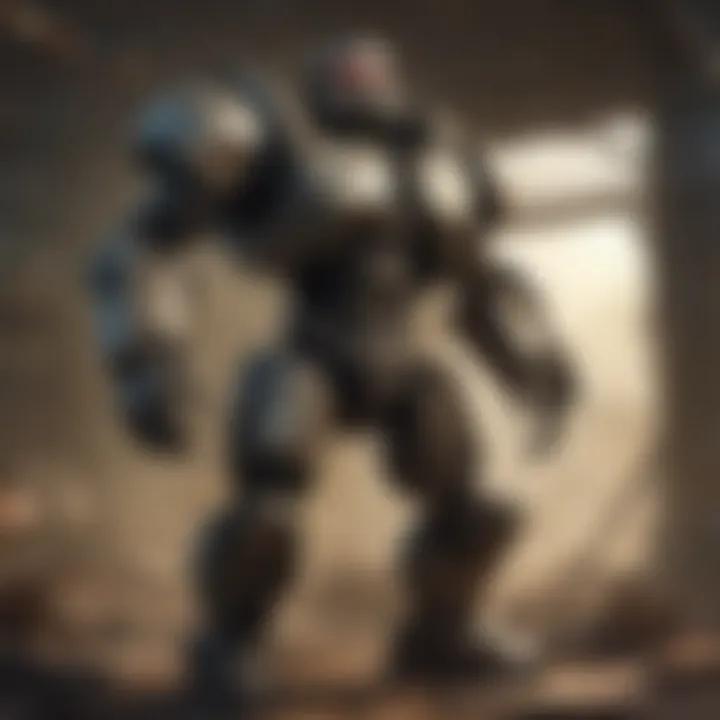
Machining with bulk steel is essential in various manufacturing processes. The key characteristic of bulk steel in machining is its machinability and precision in shaping components. Bulk steel's unique feature in machining lies in its ability to withstand high temperatures and pressures, making it ideal for precise cutting and shaping. However, the drawback of machining bulk steel is the need for specialized tools and expertise, impacting production costs.
Fabrication
Fabrication is another critical aspect where bulk steel plays a central role. The key characteristic of bulk steel in fabrication is its formability and versatility in creating customized components. Bulk steel's unique feature in fabrication lies in its adaptability to different shapes and sizes, allowing for complex structures to be manufactured. Nonetheless, the challenge of working with bulk steel in fabrication is the requirement for skilled labor and advanced equipment, which can increase production timelines and costs.
Advantages of Bulk Steel for Manufacturing
Bulk steel offers a multitude of advantages that make it a preferred choice in various industries. Its inherent strength, durability, versatility, and cost-efficiency make it a valuable material for manufacturing processes. Understanding these advantages is crucial for appreciating the role of bulk steel in modern production methods.
Strength and Durability
When it comes to the strength and durability of bulk steel, two key aspects stand out: high tensile strength and longevity.
High Tensile Strength
High tensile strength is a defining characteristic of bulk steel, making it exceptionally resilient to external forces. This property enables structures and components made from bulk steel to withstand heavy loads and harsh environments. The high tensile strength of bulk steel ensures the longevity and reliability of manufactured items, contributing to their overall quality and performance.
Longevity
The longevity of bulk steel products is another significant advantage that enhances their appeal in manufacturing. Due to its resistance to wear, corrosion, and degradation, bulk steel items have a prolonged lifespan compared to alternative materials. This longevity reduces the need for frequent replacements or repairs, resulting in cost savings and operational efficiency for industrial applications.
Versatility
Bulk steel's versatility is a key factor in its widespread adoption across different industries and applications.
Adaptability to Various Applications
The ability of bulk steel to adapt to a wide range of applications is a testament to its versatility. From automotive and construction projects to machinery and infrastructure development, bulk steel can be shaped and modified to suit diverse requirements. This adaptability makes bulk steel a versatile choice for manufacturers seeking reliability and flexibility in their production processes.
Ease of Modification
The ease of modifying bulk steel further enhances its versatility in manufacturing. Whether it's cutting, welding, or forming, bulk steel can be readily shaped and customized to meet specific design specifications. This flexibility streamlines production processes and enables rapid prototyping and innovation in various industries.
Cost-Efficiency
In addition to its inherent properties, bulk steel is known for its cost-efficiency, making it a sustainable choice for manufacturers.
Affordability
The affordable nature of bulk steel makes it an attractive option for budget-conscious projects. Its relatively low production costs and abundance in the market contribute to cost-effective manufacturing solutions. Despite being cost-effective, bulk steel maintains high quality and performance standards, offering a compelling value proposition for businesses.
Reduced Maintenance Costs
One of the significant benefits of bulk steel is its reduced maintenance costs over the long term. Its durability and resistance to wear and tear minimize the need for frequent repairs and upkeep, resulting in operational cost savings. By choosing bulk steel, manufacturers can enjoy lower maintenance expenses without compromising on the reliability and longevity of their products.
Challenges in Bulk Steel Usage
In the realm of manufacturing, challenges in bulk steel usage play a pivotal role in shaping production outcomes. Understanding and mitigating these challenges are crucial for ensuring the efficiency and quality of manufactured products. Bulk steel faces various hurdles in its utilization, ranging from corrosion issues to fabrication complexities. By addressing these challenges proactively, manufacturers can enhance the resilience and longevity of steel-based components, ultimately benefiting industries such as automotive, construction, and beyond.
Corrosion Resistance
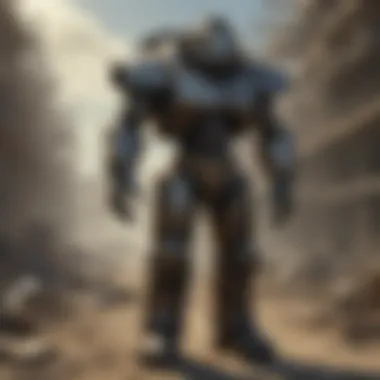
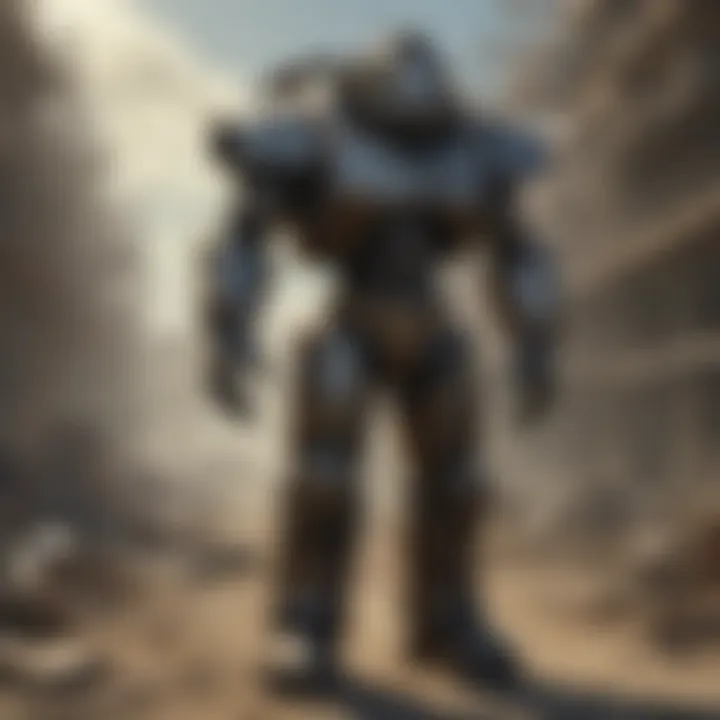
Corrosion resistance stands as a critical aspect in the use of bulk steel, particularly in environments prone to oxidation. Protective coatings provide a shield against corrosive elements, safeguarding the integrity of steel structures. One prominent characteristic of protective coatings is their ability to form a barrier that impedes the entry of moisture and other corrosive agents. This feature is instrumental in preventing rust and prolonging the lifespan of steel materials, making protective coatings a preferred choice in industries where corrosion poses a significant threat. However, while protective coatings offer excellent protection, their application and maintenance can be demanding, requiring specialized skills and adherence to maintenance schedules to ensure long-lasting effectiveness.
Regular Maintenance
Regular maintenance of bulk steel structures is indispensable in upholding their performance and longevity over time. Scheduled inspections, cleaning, and repairs constitute the essence of effective maintenance practices. One key characteristic of regular maintenance is its proactive nature, enabling the early detection of potential issues before they escalate. This proactive approach not only extends the lifespan of steel components but also reduces the likelihood of costly repairs or replacements. While regular maintenance offers significant advantages in terms of structural integrity and operational reliability, it requires dedication and resources to sustain. Balancing the costs and benefits of regular maintenance is essential for maximizing the overall value derived from bulk steel applications.
Complexity in Fabrication
Fabricating bulk steel components involves intricate processes that demand specialized equipment and skilled labor. From shaping steel plates to welding complex structures, fabrication presents challenges that require advanced tools and techniques. Specialized equipment requirements, including cutting tools, welding machines, and forming panels, are essential for precise and efficient steel fabrication. The key characteristic of specialized equipment lies in its ability to handle large-scale steel processing tasks with accuracy and consistency, contributing to the quality and durability of final products. While the use of specialized equipment streamlines production processes, it also necessitates trained operators and maintenance procedures to ensure optimal performance and safety standards.
Skilled Labor
The role of skilled labor in bulk steel fabrication cannot be understated, as human expertise drives the precision and craftsmanship required in manufacturing. Skilled workers possess the knowledge and proficiency to operate specialized equipment, interpret technical drawings, and execute intricate fabrication procedures. The key characteristic of skilled labor lies in its adaptability to diverse fabrication challenges, enabling innovative solutions and high-quality outcomes. While skilled labor enhances the efficiency and accuracy of steel fabrication, it also requires ongoing training and development to keep pace with technological advancements and industry demands. Investing in skilled labor not only improves production efficiency but also fosters a culture of excellence and innovation in bulk steel manufacturing processes.
Future Trends in Bulk Steel
In this segment, we will delve into the future trends in bulk steel, a pivotal aspect of the manufacturing landscape. These trends play a crucial role in shaping the evolution of steel production and utilization in various industries. Understanding the trajectory of bulk steel is essential for stakeholders to anticipate changes, innovations, and challenges in the sector. By exploring future trends, we can discern the technological advancements, market demands, and environmental considerations that will influence the journey of bulk steel in the coming years.
Innovations in Steel Alloying
Nanotechnology Integration
Nanotechnology integration represents a groundbreaking advancement in steel alloying. This intricate process involves incorporating nanoscale materials into steel matrices to enhance its properties. The key characteristic of nanotechnology integration lies in its ability to manipulate steel at the atomic and molecular levels, leading to remarkable improvements in strength, durability, and performance. This innovative approach is gaining traction in the industry due to its potential for creating customized steel formulations with superior characteristics tailored to specific applications. Despite its promising advantages, nanotechnology integration also presents challenges related to scalability, cost-effectiveness, and potential environmental impacts that need thorough consideration.
Advanced Metallurgical Techniques
Advanced metallurgical techniques offer a sophisticated means of refining bulk steel for enhanced functionality and efficiency. These techniques involve intricate processes such as controlled heating, cooling, and alloying to achieve desired mechanical and chemical properties in steel. The key characteristic of advanced metallurgical techniques is their precision and control over the steel composition and structure, resulting in optimized performance for diverse applications. This approach is favored for its ability to produce high-quality steel with exceptional characteristics that meet stringent industry requirements. While advanced metallurgical techniques offer a pathway to innovation and quality improvement, they also require specialized expertise, equipment, and resources, posing challenges in implementation and scalability.
Sustainable Steel Production
In the realm of sustainable steel production, two critical aspects come to the forefront: recycling initiatives and carbon-neutral practices. These initiatives aim to minimize the environmental footprint of steel manufacturing while ensuring long-term viability and eco-friendliness in the industry.
Recycling Initiatives
Recycling initiatives emphasize the importance of circular economy principles in steel production. By recycling scrap steel and reprocessing it into new products, these initiatives reduce energy consumption, raw material usage, and waste generation in the manufacturing process. The key characteristic of recycling initiatives is their ability to promote resource efficiency, cost savings, and environmental conservation through a closed-loop approach. While recycling steel offers compelling benefits in terms of sustainability and resource preservation, challenges exist in efficiently collecting, sorting, and processing scrap steel into viable raw materials for steel production.
Carbon Neutral Practices
Carbon-neutral practices are instrumental in mitigating the carbon footprint of steel manufacturing operations. By adopting low-carbon technologies, renewable energy sources, and carbon offsetting measures, companies can strive towards achieving carbon neutrality in their production processes. The key characteristic of carbon-neutral practices is their focus on reducing greenhouse gas emissions, promoting clean energy utilization, and enhancing overall environmental stewardship in the steel industry. While carbon-neutral practices hold significant advantages for sustainability and climate change mitigation, the transition to carbon neutrality entails financial investments, technological upgrades, and operational adjustments that may pose challenges for some enterprises.
Conclusion
Bulk steel plays a pivotal role in the manufacturing industry, serving as a cornerstone for a multitude of applications. Its importance cannot be overstated, as it provides the backbone for structures and components in various sectors, ensuring strength, durability, and reliability. The versatile nature of bulk steel allows for its use in diverse applications, ranging from automotive manufacturing to construction projects.
Summary of Key Points
Importance of Bulk Steel
Bulk steel's significance lies in its exceptional strength and durability. As a trusted material in manufacturing, it offers high tensile strength and longevity, making it a preferred choice for industrial purposes. The ability of bulk steel to adapt to different applications and undergo modifications with ease further enhances its appeal, proving to be a cost-effective solution for various industries.
Diverse Applications
The diverse applications of bulk steel underscore its adaptability and reliability. Whether in the automotive industry for vehicle manufacturing or in the construction sector for building structures, bulk steel remains a primary choice for its structural integrity and performance. Its versatility in machining and fabrication processes showcases its flexibility and efficiency in meeting specific manufacturing requirements.
Future Prospects
Looking ahead, the future prospects of bulk steel continue to evolve with innovations in steel alloying and sustainable production practices. Through the integration of nanotechnology and advanced metallurgical techniques, bulk steel is poised to become even stronger and more resilient. Embracing recycling initiatives and carbon-neutral practices, the industry is moving towards a more sustainable future, ensuring the longevity and eco-friendliness of bulk steel production.