Unveiling the Intricacies of a Crushing Plant and Its Operations
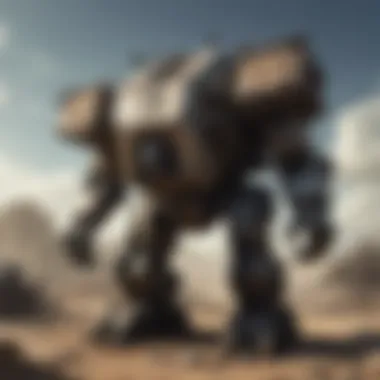
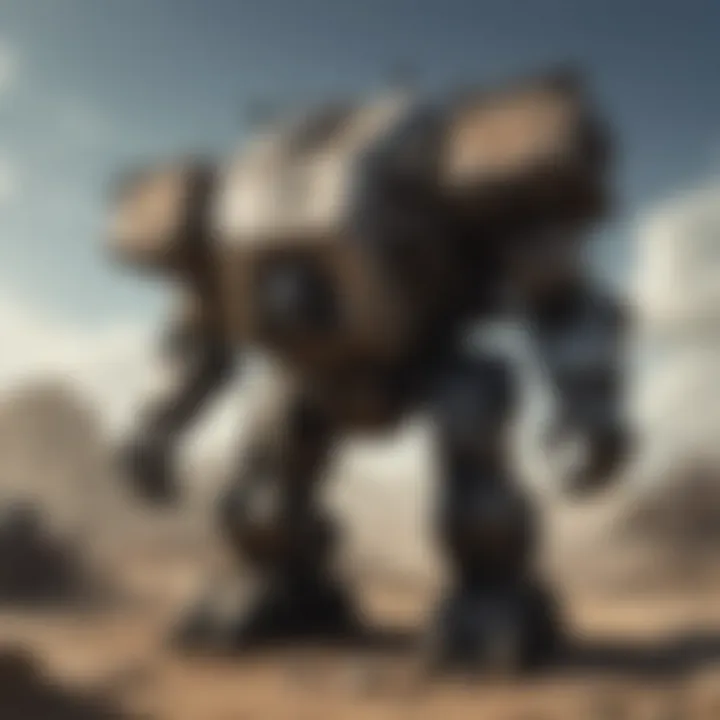
Lore Insights
In the realm of crushing plants, the intricate machinery and processes at play mirror the complexities witnessed in the Fallout universe. Just as key historical events shaped the course of factions and characters in Fallout, understanding the foundational elements of a crushing plant is vital. From the primary crushing stage resembling the origin story to the tertiary stage symbolizing character evolution, parallels can be drawn to enhance comprehension.
Gameplay Tips and Strategies
Navigating the operations of a crushing plant can be likened to maneuvering through the treacherous wasteland in Fallout games. Just as a beginner in Fallout games seeks guidance, individuals delving into crushing plant operations require a primer on efficient resource management. Drawing weapon and armor recommendations as analogies, optimizing processes for maximum output becomes the primary goal.
Character Analysis
In a crushing plant's ecosystem, each component fulfills a role much like iconic characters in the Fallout series. Detailed profiles of these components shed light on their significance in the overall operational framework. Exploring relationships between these components mirrors the complex character dynamics within Fallout, drawing a parallel between mechanical efficiency and character development.
News and Updates
Staying abreast of the latest developments in both the crushing plant industry and the Fallout series is paramount. Just as game developers release patch notes and DLC updates, innovations in crushing plant technology affect operational strategies. Community events and tournaments reflect the shared enthusiasm within respective realms, indicating a continuous evolution in both industries.
Fan Theories and Speculations
Just as fans dissect the Fallout universe for hidden clues, operators in the crushing plant domain often speculate on future advancements. Unraveling popular fan theories fosters a culture of innovation and exploration, much like the anticipation surrounding future Fallout installments. The convergence of speculation between these seemingly disparate worlds underscores the depth of analysis required for sustained growth and progress.
Prologue to Crushing Plant
Delving into the realm of crushing plants unveils a complex web of machinery and processes that drive key industries such as mining, construction, and aggregate production. This section serves as a foundational piece of the article, laying the groundwork for understanding the fundamental aspects of how a crushing plant functions within industrial operations. By shedding light on the critical components, functions, and operational intricacies, we aim to provide a holistic view of the pivotal role played by crushing plants.
Definition and Purpose
Understanding the concept of a crushing plant
Exploring the concept of a crushing plant exposes the core principles that underpin its functionality. From the utilization of various crushing equipment to the systematic processes involved, understanding this concept is paramount to deciphering its significance in industrial settings. The adaptability and efficiency of crushing plants in processing raw materials make them a popular choice across sectors like mining, construction, and manufacturing. The unique feature lies in their ability to break down bulk materials into smaller particles, facilitating further downstream operations seamlessly.
The primary objective of a crushing plant
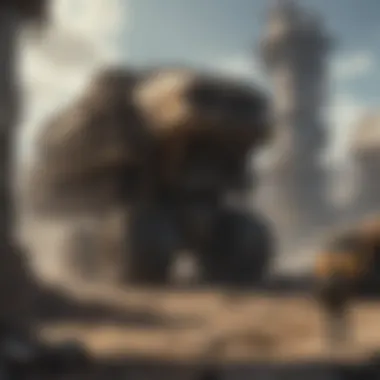
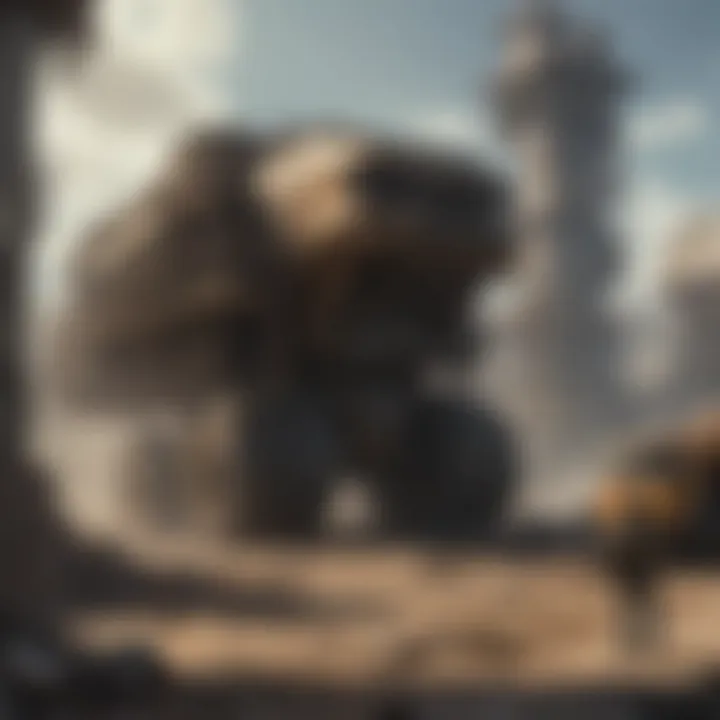
At the heart of every crushing plant lies a primary objective โ to efficiently crush and process raw materials to meet specific industry requirements. This primary function forms the backbone of operations within the plant, ensuring a streamlined approach to material processing. The primary objective emphasizes the plant's role in optimizing material size reduction and shaping processes. While advantageous in enhancing operational efficiency, it also presents challenges in terms of maintenance and resource utilization.
Significance in Industries
Impact of crushing plants in the mining sector
The impact of crushing plants in the mining sector resonates deeply with the industry's core operations. By enabling the extraction and processing of valuable minerals, these plants contribute significantly to the sector's productivity and profitability. The key characteristic lies in their ability to handle diverse mineral compositions, offering tailored solutions to meet varying demands within the mining landscape. Despite their undeniable advantages, challenges such as high energy consumption and equipment maintenance persist within this arena.
Relevance of crushing plants in construction
Crushing plants hold immense relevance in the construction industry, where they play a vital role in processing aggregates for various construction projects. The pivotal characteristic of these plants is their ability to produce a range of aggregate sizes to suit different building requirements, enhancing construction efficiency. Their unique feature lies in their versatility, adapting to different material types and project specifications. However, issues like environmental impact and transportation costs pose significant considerations for construction firms utilizing crushing plants.
Components of a Crushing Plant
In the intricate world of crushing plants, understanding the components forms the bedrock of efficient operations. The primary components that drive the functioning of a crushing plant are jaw crushers, gyratory crushers, and impact crushers, each playing a vital role in the crushing process. Auxiliary equipment such as conveyors, feeders, and screens complement the primary components, ensuring a smooth and continuous operation. These components not only enhance productivity and output but also contribute significantly to the safety and maintenance of the crushing plant.
Primary Components
Jaw crushers
Jaw crushers, a cornerstone of crushing plants, excel in their ability to conduct primary crushing stages effectively. Their robust design and versatile nature make them a preferred choice across various industries. With their unique feature of adjustable settings, jaw crushers offer a customizable solution for different materials, enhancing the plant's flexibility. Although jaw crushers boast high efficiency, they may require regular maintenance due to their mechanical complexity.
Gyratory crushers
Gyratory crushers, another primary component, excel in handling large feed sizes and achieving high reduction ratios. Their key characteristic lies in their ability to crush materials with high hardness efficiently. The primary advantage of gyratory crushers is their capability to process large quantities of material, making them ideal for heavy-duty applications. However, their main drawback is the higher initial cost compared to other crushers.
Impact crushers
Within crushing plants, impact crushers stand out for their ability to deliver high reduction ratios in the secondary crushing stage. Their key characteristic lies in their unique rotor design, which ensures a high reduction rate and superior particle shape. Impact crushers are popular for their high productivity and low operating costs, making them a valuable asset for enhancing overall plant efficiency. Despite their advantages, impact crushers may produce more fines than other crushers, requiring careful management.
Auxiliary Equipment
Conveyors
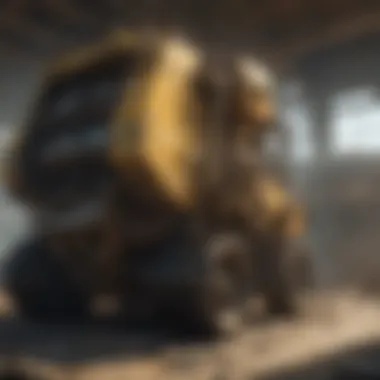
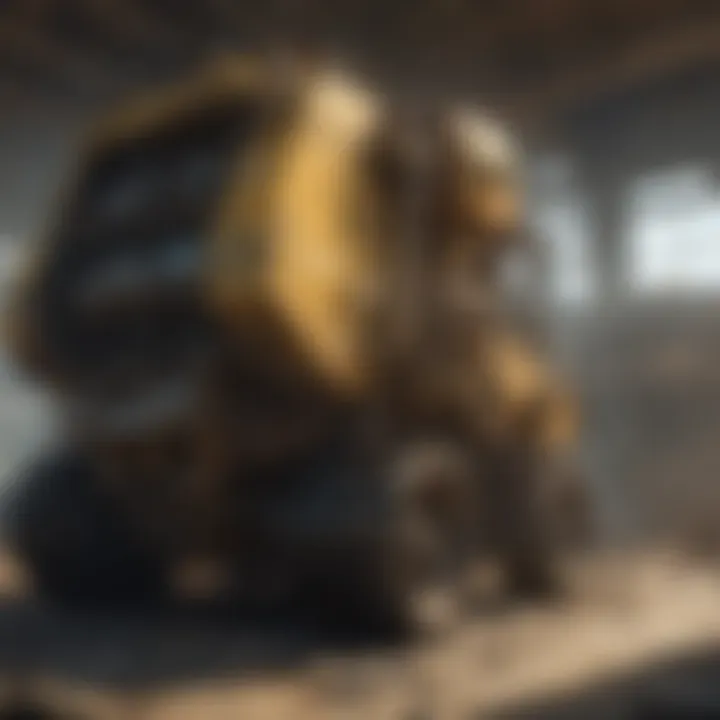
Conveyors, essential auxiliary equipment, play a crucial role in material transport within crushing plants. Their key characteristic of continuous operation ensures seamless material flow, minimizing downtime. Conveyors are beneficial for optimizing productivity by transferring materials efficiently between different stages of the crushing process. However, their reliance on electrical systems poses a risk of potential breakdowns, necessitating regular monitoring and maintenance.
Feeders
Feeders, vital companions to crushing plants, facilitate a controlled and steady supply of material to the crushing equipment. Their key characteristic lies in their adjustable feed rates, allowing operators to optimize material flow as per requirements. Feeders are popular for their ability to prevent choking of the crushing equipment, ensuring a consistent and reliable operation. Despite their benefits, feeders may require frequent adjustments to accommodate varying material characteristics.
Screens
Screens, integral auxiliary components, enhance the efficiency of crushing plants by segregating materials of different sizes. Their key characteristic of customizable screening options offers plant operators flexibility in managing material output. Screens are instrumental in maximizing the plant's productivity by separating fines early in the process and optimizing material distribution. However, screens may face issues like clogging, requiring regular cleaning and maintenance for uninterrupted operation.
Operation of a Crushing Plant
In the intricate web of a crushing plant's functionality, the operation stands as a critical node. It serves as the heartbeat, driving the entire process forward towards the desired outcomes. Understanding the operation of a crushing plant is akin to deciphering a complex puzzle - each piece essential for the bigger picture. From the primary crushing stage to the tertiary crushing stage, every operation within the plant plays a pivotal role. The operation is not just about executing tasks but about orchestrating a symphony of actions aimed at achieving efficiency, productivity, and quality output. Control systems, monitoring mechanisms, and human intervention converge in harmony to ensure seamless operation, where precision and timing are of the essence. Unveiling the layers of the operation of a crushing plant unveils the core essence of industrial processes, with safety and optimization as cornerstone principles.
Crushing Process
Primary crushing stage
At the forefront of the crushing process stands the primary crushing stage, a robust and foundational element in the plant's operations. This phase sets the tone for subsequent stages, being the initial step in breaking down raw materials into manageable sizes. Primary crushers like jaw crushers and gyratory crushers are the workhorses handling the brunt of coarse crushing tasks, reducing oversized rocks into more manageable fragments. Their rugged construction and high throughput capacity make them a preferred choice for handling large volumes of materials efficiently. While primary crushing expedites the material preparation process, it also poses challenges like potential blockages and uneven feed distribution, demanding meticulous operational oversight.
Secondary crushing stage
Following the primary crushing stage is the secondary crushing stage, where finer reduction of materials takes place to achieve the desired product specifications. Impact crushers come into play during this phase, finely crushing the pre-processed material from the primary stage. The key characteristic of the secondary crushing stage lies in its ability to produce graded aggregates required for various industry applications. Its versatility in producing different product sizes makes it a valuable asset in maximizing the plant's overall output. However, the secondary stage demands precise control to maintain product quality, as excessive crushing can lead to product degradation or high fines content.
Tertiary crushing stage
The tertiary crushing stage stands as the final frontier in the crushing process, adding the finishing touches to the material before it is ready for its designated application. Tertiary crushers refine the material even further, producing fine aggregates for specialized purposes like concrete production or road construction. The key feature of the tertiary stage is its role in shaping the final product characteristics, enhancing gradation and particle shape for optimized performance. While offering superior product quality, the tertiary crushing stage requires careful monitoring to prevent over-crushing, which can result in excessive fines generation and reduced overall efficiency.
Control and Monitoring
Automation systems
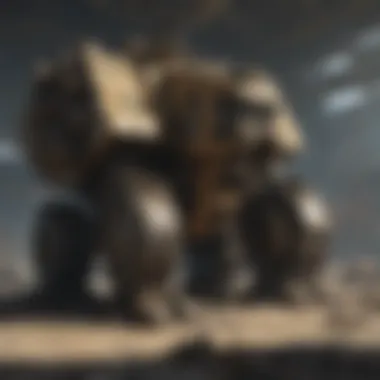
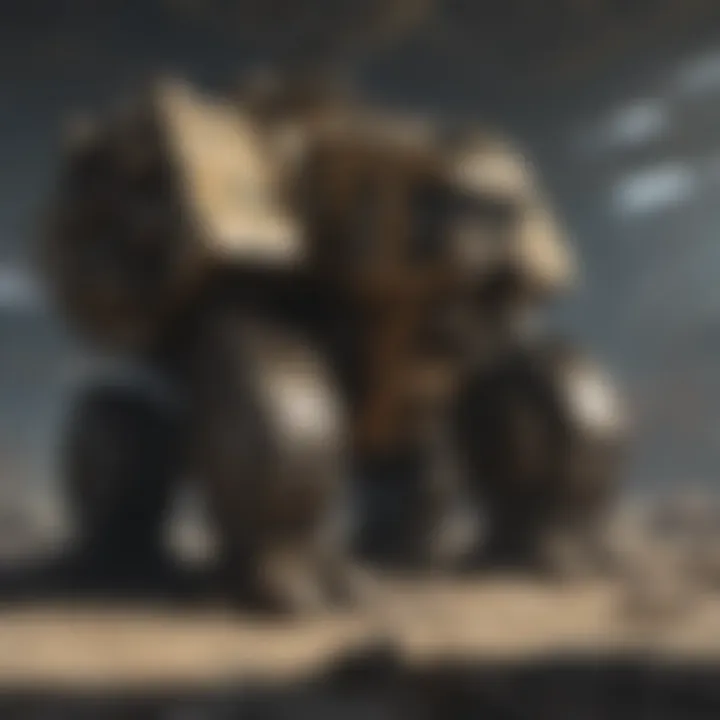
Automation systems form the nerve center of a modern crushing plant's control and monitoring infrastructure, revolutionizing how operations are managed with precision and efficiency. By automating processes like crusher adjustment, material feeding, and plant optimization, automation systems elevate the performance and productivity of the plant. The key characteristic of automation systems lies in their ability to streamline operations, reduce human intervention, and enhance safety by minimizing manual errors. Their unique feature of real-time data analysis empowers operators with actionable insights, enabling proactive decision-making to maximize plant efficiency while maintaining product quality.
Real-time monitoring
Real-time monitoring plays a vital role in ensuring the smooth operation of a crushing plant, providing instantaneous feedback on critical parameters for timely intervention. By continuously monitoring factors like crusher settings, material flow, and equipment status, real-time monitoring enables operators to preempt potential issues and optimize plant performance. The key characteristic of real-time monitoring is its ability to offer instantaneous feedback, allowing for rapid adjustments to maintain operational efficiency. Its unique feature of early fault detection enhances equipment reliability and minimizes downtime, contributing to overall productivity. While real-time monitoring offers significant benefits, such systems require regular calibration and maintenance to ensure accurate data acquisition and optimal performance.
Maintenance and Safety Protocols
Regular Maintenance Practices
- Inspections: Within the landscape of regular maintenance practices, inspections stand out as a pivotal aspect in upholding the operational integrity of a crushing plant. These thorough examinations serve to identify any potential issues or wear and tear within the machinery, allowing for timely intervention and preventive maintenance. Inspections play a crucial role in enhancing the overall reliability and performance of the crushing plant, making them an indispensable practice in this context.
- Lubrication routines: Another critical element in regular maintenance practices is the implementation of effective lubrication routines. Proper lubrication is essential for ensuring smooth operation and reducing frictional wear on moving parts. By incorporating appropriate lubrication routines, operators can significantly extend the lifespan of components, optimize performance, and diminish the likelihood of costly breakdowns. The meticulous application of lubricants is a cornerstone of maintenance practices in the realm of crushing plants.
- Wear part replacements: When it comes to maintaining a crushing plant, the timely replacement of wear parts emerges as a key focus area. As components undergo regular wear and tear during operation, proactive replacement of worn-out parts is crucial for sustaining optimal performance levels. By promptly addressing wear part replacements, operators can prevent operational disruptions, uphold efficiency, and prolong the overall lifespan of the crushing plant.
Safety Measures
- Training protocols: In the domain of safety measures, comprehensive training protocols play a fundamental role in mitigating risks and promoting a secure working environment within the crushing plant. Equipping personnel with the requisite knowledge and skills ensures that operations are conducted in accordance with best practices and safety standards. Training protocols not only enhance employee competency but also contribute to accident prevention and regulatory compliance, making them indispensable for fostering a culture of safety within the workplace.
- Emergency procedures: Complementing training protocols, emergency procedures are a critical component of safety measures in a crushing plant setting. Establishing clear and effective protocols for handling emergencies or unforeseen events is essential for safeguarding personnel and mitigating potential hazards. By outlining detailed emergency procedures and conducting regular drills, operators can minimize response times, mitigate damage, and promote a culture of preparedness and safety awareness within the facility.
Optimizing Crushing Plant Performance
In the realm of crushing plants, optimizing performance is paramount for efficient operations and maximal output. This section delves deep into strategies and techniques aimed at enhancing the overall functionality of a crushing plant. By focusing on optimization, industries such as mining, construction, and aggregate production can significantly boost their productivity and cost-effectiveness. The overarching goal is to fine-tune every aspect of the crushing process to achieve optimal results, making it a cornerstone of successful plant management.
Efficiency Enhancement Strategies
Adjusting CSS
Adjusting CSS (Closed Side Setting) stands out as a crucial aspect in the optimization of crushing plant performance. By precisely adjusting the CSS of crushers, operators can control the product size and shape, contributing to improved overall efficiency and quality of the produced material. This strategy enables tailored adjustments to match specific requirements, ensuring that the crushing plant operates at its peak efficiency levels. While the process can be meticulous, the benefits of CSS adjustment are undeniable, offering unparalleled control over the crushing parameters for enhanced performance.
Optimizing feed
Optimizing feed plays a pivotal role in maximizing the efficiency of a crushing plant. By fine-tuning the feeding process, operators can regulate the flow of materials into the crushers, optimizing throughput and reducing bottlenecks. This strategic approach helps in achieving a balanced and consistent feed rate, minimizing variations and ultimately enhancing the overall performance of the plant. The optimization of feed not only boosts productivity but also ensures the longevity of the equipment, making it a fundamental element in enhancing crushing plant operations.
Output Maximization Techniques
Maintaining ideal choke feeding
Maintaining ideal choke feeding is key to maximizing the output of a crushing plant. This technique involves keeping the crushing chamber at full capacity to ensure continuous and efficient crushing. By controlling the feed rate and optimizing the cavity level, operators can prevent overloading the crusher and achieve a steady flow of material, leading to higher throughput and product quality. While demanding attention to detail, ideal choke feeding presents substantial advantages by promoting consistent operation and reducing the risk of downtime.
Utilizing automation for consistency
Utilizing automation for consistency revolutionizes the way crushing plants operate. Automation systems streamline processes, ensuring uniformity in operations and reducing human error. By incorporating automation, plants can achieve consistent performance levels, enhance throughput, and optimize resource utilization. While initial setup may require investment, the long-term benefits include increased efficiency, reduced maintenance costs, and improved safety standards. The integration of automation paves the way for seamless plant control and sets new standards for performance optimization.