Unlocking the Potential: Strategies to Optimize Conveyor Lift Systems for Peak Performance
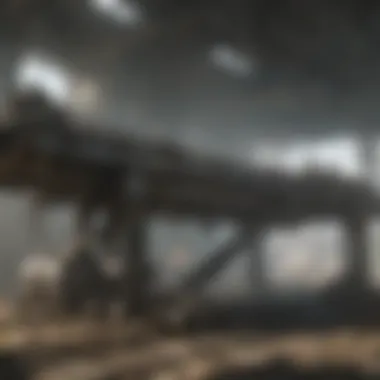
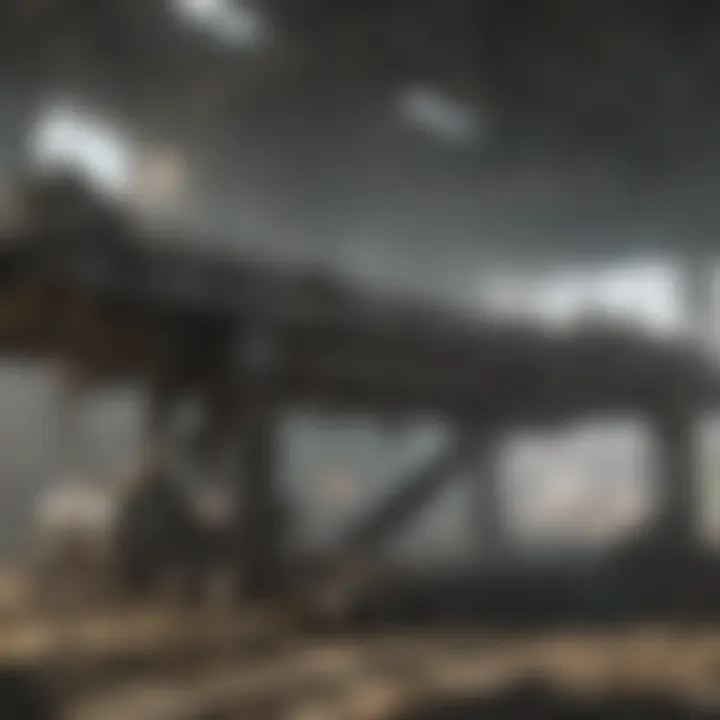
Lore Insights
Gameplay Tips and Strategies
One of the fundamental aspects of optimizing conveyor lift systems is to ensure efficient resource management. From selecting the appropriate conveyor belt types to strategically positioning the lifts, every decision can impact the system's efficiency. Additionally, considering tips for better material handling, maintaining equipment, and monitoring performance metrics can further contribute to enhancing productivity. By delving into advanced strategies and best practices, readers can unlock the full potential of their conveyor lift systems and achieve maximum efficiency in their operations.
Character Analysis
In the context of conveyor lift systems, analyzing the different components and their interactions can be likened to examining the relationships between characters in a narrative. Just as characters evolve and develop across a storyline, conveyor lift systems undergo transformations through optimization efforts. By focusing on detailed profiles of key components, such as motors, belts, and controls, readers can gain a deeper understanding of how these elements work together harmoniously to support the system's functionality. Furthermore, exploring the evolution of conveyor lift technology across different industries can provide valuable insights into its future potential and innovative applications.
News and Updates
Keeping abreast of the latest advancements in conveyor lift technology is crucial for organizations seeking to optimize their systems and stay ahead of the curve. By staying informed about industry developments, such as new product releases, updates, and upcoming events, readers can gain a competitive edge and make informed decisions about incorporating the latest innovations into their operations. Monitoring manufacturers' announcements, industry trends, and customer feedback can offer valuable perspectives on the evolving landscape of conveyor lift systems and opportunities for improvement.
Fan Theories and Speculations
In the realm of conveyor lift optimization, exploring fan theories and speculations can spark creativity and innovation in problem-solving. By embracing a speculative mindset and pondering potential future advancements in lift system efficiency, readers can engage in thought-provoking discussions that challenge conventional thinking. Considering unresolved challenges and brainstorming innovative solutions can lead to groundbreaking discoveries and strategies for optimizing conveyor lift systems to unprecedented levels of efficiency.
Introduction to Conveyor Lift Systems
In the realm of material handling systems, the introduction of conveyor lift systems has revolutionized efficiency and productivity in various industries. These systems play a crucial role in streamlining operations, transporting goods vertically with precision and speed. By incorporating conveyor lift systems, organizations can optimize their logistical processes, reduce manual labor, and enhance overall workflow efficiency.
Definition and Purpose
1. Understanding the Role of Conveyor Lift Systems
The primary function of conveyor lift systems is to vertically transport materials within a facility. Whether moving goods between different levels of a building or loadingunloading trucks at varying heights, these systems provide a seamless solution for material handling challenges. Their versatility and reliability make them a popular choice for warehouses, manufacturing plants, and distribution centers seeking to enhance operational efficiency.
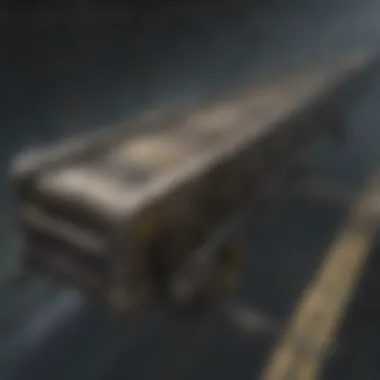
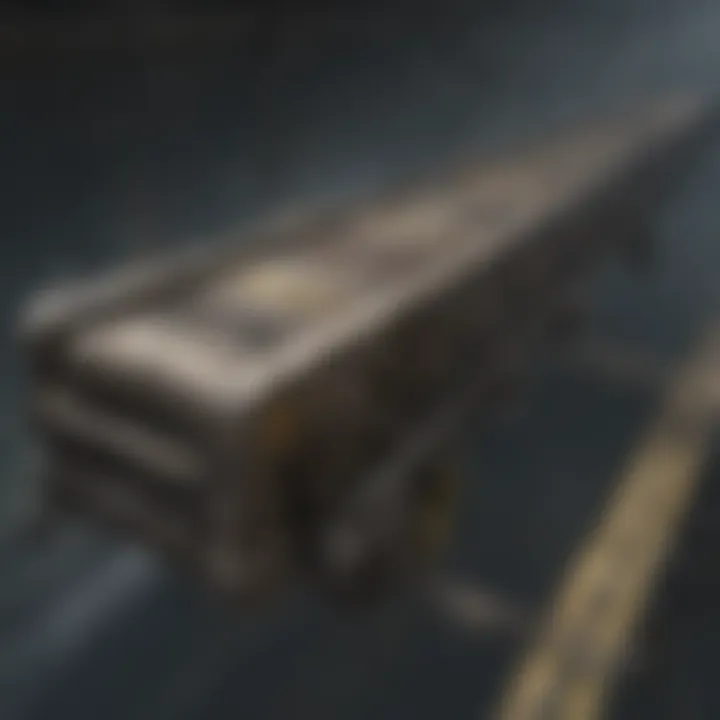
Conveyor lift systems are characterized by their ability to efficiently move heavy loads, bulky items, and fragile goods with minimal human intervention. This automation not only accelerates the material flow but also reduces the risk of manual handling injuries and errors. This key feature makes conveyor lift systems an indispensable asset for enhancing productivity within the context of this article.
2. Importance of Efficient Material Handling
Efficient material handling is essential for optimizing the overall workflow within any industrial setting. The timely and accurate movement of raw materials, components, or finished products is a critical aspect of operational success. Conveyor lift systems significantly contribute to streamlining this process by ensuring smooth and continuous transport of materials, thereby minimizing downtime and maximizing output.
The strategic deployment of conveyor lift systems aids in reducing material handling costs, improving inventory management, and enhancing resource utilization. By promoting a more organized and systematic approach to material movement, these systems help businesses meet production schedules, fulfill orders promptly, and maintain high levels of customer satisfaction. The emphasis on efficient material handling is paramount in the context of this article, highlighting its pivotal role in operational excellence.
Types of Conveyor Lift Systems
1. Vertical Reciprocating Conveyors (VRCs)
Vertical Reciprocating Conveyors, or VRCs, are specifically designed to move materials vertically between various levels of a facility. Unlike traditional conveyors that move materials horizontally, VRCs offer a versatile solution for handling goods in confined spaces or multi-level buildings. Their space-saving design and customizable features make them a preferred choice for businesses aiming to maximize storage capacity and operational efficiency.
A unique feature of VRCs is their ability to transport heavy loads with ease, addressing the challenges of moving substantial materials within limited spaces. This characteristic is advantageous for industries where space optimization and ergonomic material handling are crucial. However, despite their efficiency, VRCs require regular maintenance to ensure seamless operation, which is a key consideration discussed in this article.
2. Spiral Conveyors
Spiral conveyors are innovative systems that utilize a spiral belt to transport materials vertically or horizontally in a continuous flow. These conveyor systems are ideal for applications that involve the constant elevation or declination of goods, facilitating a smooth and efficient material transfer process. The spiral design of these conveyors enables compact vertical transportation while saving valuable floor space in industrial settings.
A significant advantage of spiral conveyors is their ability to handle goods in a gentle manner, minimizing product damage during the conveying process. This gentle handling makes spiral conveyors suitable for transporting fragile items or delicate components without compromising their quality. However, it is essential to consider the operational speed and capacity limitations of spiral conveyors when optimizing material handling processes.
3. Pneumatic Vacuum Conveyors
Pneumatic vacuum conveyors operate on the principle of creating a vacuum to suction and transport materials through a closed tube system. These systems are commonly used in industries that require the gentle and dust-free handling of powdered or granular materials. Pneumatic vacuum conveyors offer a hygienic solution for transferring materials in pharmaceutical, food processing, and chemical manufacturing facilities, ensuring contamination-free transportation.
An advantage of pneumatic vacuum conveyors is their ability to transport materials over long distances without significant manual intervention, enhancing operational efficiency. Moreover, the dust-free and enclosed nature of these systems promotes a clean working environment, adhering to strict sanitation standards in industries where product purity is paramount. However, the energy consumption and maintenance requirements of pneumatic vacuum conveyors should be carefully considered to achieve optimal efficiency in material conveying processes within the context of this article.
II. Key Components of Conveyor Lift Systems
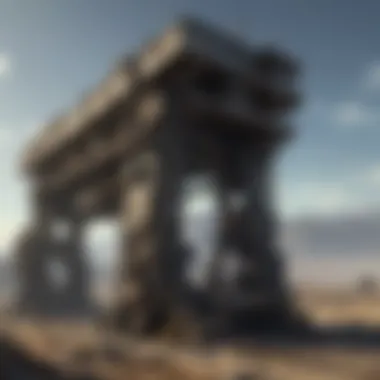
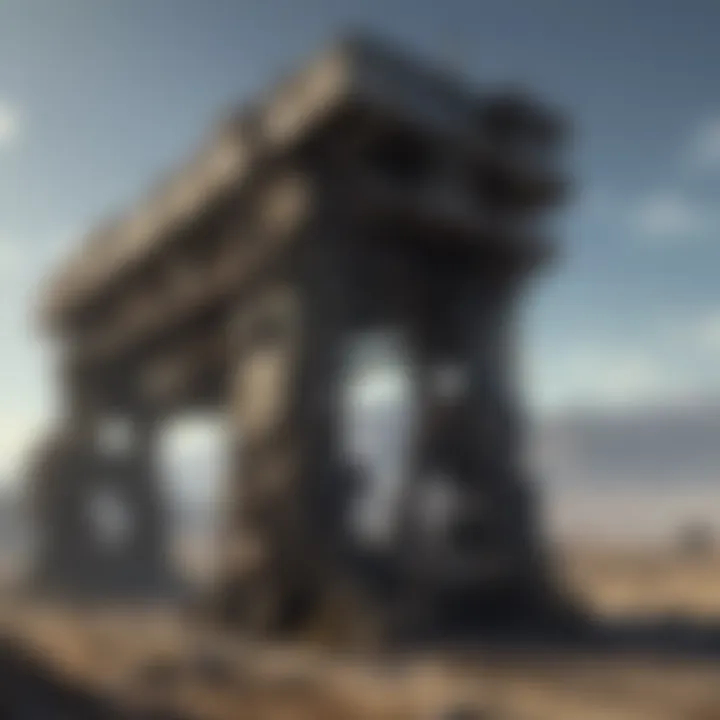
A. Drive Units and Motors
When delving into drive units and motors, one encounters the heart of a conveyor lift system. The power transmission in conveyor systems is a pivotal aspect that drives the entire operation. This transmission mechanism facilitates the movement of materials along the conveyor, ensuring a smooth and continuous workflow. The selection of suitable motors is crucial as they provide the necessary power to drive the system efficiently. Considering motor selection goes beyond mere horsepower; factors like energy efficiency, torque requirements, and maintenance needs play significant roles in ensuring optimal performance.
B. Belts, Rollers, and Pulleys
Conveyor belts come in various types, each designed for specific applications and load requirements. Selecting the right type of belt is essential for the smooth movement of materials and minimizing wear and tear. Rollers and pulleys, on the other hand, aid in guiding the belt and maintaining proper tension. Understanding the role of rollers and pulleys in conveyor systems helps in preventing slippage and ensuring consistent operation. Choosing the appropriate size, material, and configuration of rollers and pulleys is vital to avoid issues like misalignment and inefficiency in material transport.
III. Optimizing Efficiency in Conveyor Lift Systems
In this segment of the article, we explore the critical aspect of optimizing efficiency in conveyor lift systems. Efficiency plays a pivotal role in enhancing productivity and reducing operational costs, making it a focal point for industries utilizing such systems. By implementing strategic measures to streamline operations and maximize output, businesses can gain a competitive edge in their respective markets.
A. Proper Maintenance Practices
1. Lubrication and Inspection Procedures
Delving into lubrication and inspection procedures reveals a fundamental maintenance practice that impacts the overall performance of conveyor lift systems. Regular lubrication and thorough inspection not only ensure smooth operation but also extend the lifespan of critical components. The choice to prioritize lubrication and inspection stems from its proven track record in minimizing downtime and preventing costly breakdowns. One unique feature of this practice is its ability to proactively address potential issues before they escalate, leading to improved operational efficiency and reduced maintenance expenses.
2. Preventive Maintenance Scheduling
Preventive maintenance scheduling is another key aspect in optimizing the efficiency of conveyor lift systems. By adhering to a well-structured maintenance schedule, businesses can mitigate the risk of unexpected failures and optimize system performance. The proactive nature of preventive maintenance scheduling allows for planned downtime, reducing the chances of unplanned disruptions during peak operational periods. Its unique feature lies in its ability to forecast maintenance needs based on usage patterns, ultimately enhancing system reliability and operational continuity.
B. Load Management Techniques
1. Balancing Loads for Even Distribution
Balancing loads for even distribution is a strategic approach to optimizing conveyor lift system efficiency. By ensuring that loads are evenly distributed, businesses can prevent issues such as overloading specific sections or uneven wear on components. This technique is a popular choice for its ability to maximize conveyor system lifespan and minimize the risk of malfunctions. Its unique feature lies in its capacity to promote smooth and consistent operation, leading to enhanced overall efficiency and reduced maintenance requirements.
2. Overload Prevention Strategies
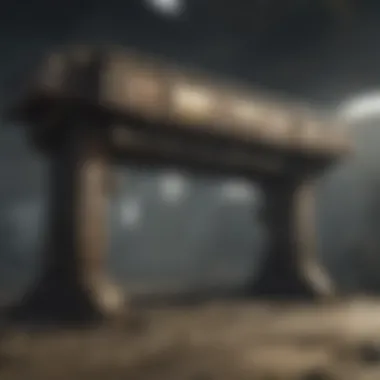
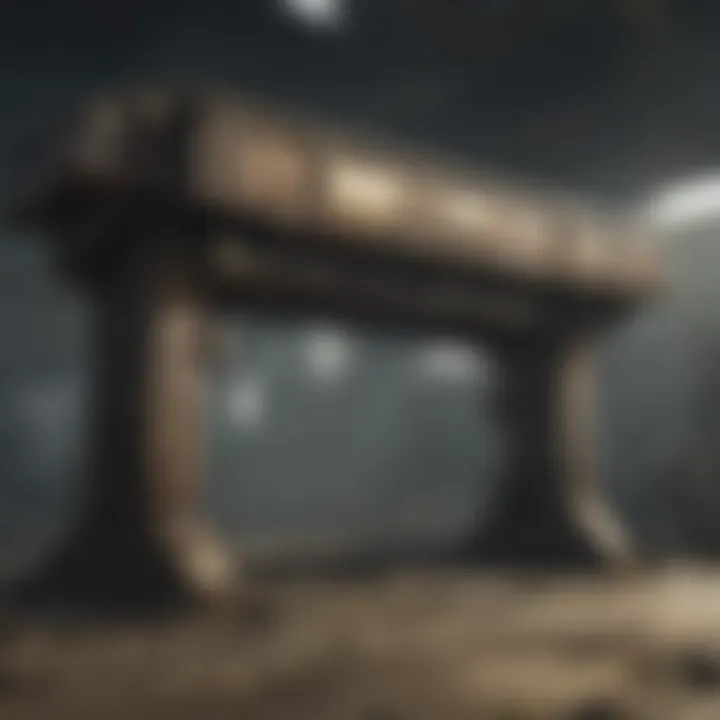
Overload prevention strategies are paramount in maintaining the efficiency of conveyor lift systems. By implementing measures to prevent overloading, businesses can safeguard against system failures, reduce safety risks, and protect valuable cargo. The key characteristic of these strategies is their ability to optimize workflow by preventing bottlenecks and ensuring consistent performance. The unique feature of overload prevention strategies is their proactive nature, which anticipates potential issues and safeguards system integrity, contributing to enhanced operational efficiency and improved safety standards.
C. Automation and Control Systems
1. Integration of Sensors and PLCs
The integration of sensors and programmable logic controllers (PLCs) underscores a pivotal advancement in enhancing conveyor lift system efficiency. By leveraging sensors for real-time data monitoring and PLCs for automated control, businesses can optimize operational processes and adapt dynamically to changing demands. This integration is a beneficial choice for its capacity to streamline operations, increase system responsiveness, and reduce manual interventions. A unique feature of sensor and PLC integration is their role in facilitating predictive maintenance and data-driven decision-making, enhancing overall system efficiency and sustainability.
2. Automated Sorting and Routing
Automated sorting and routing capabilities significantly contribute to improving efficiency in conveyor lift systems. By automating the sorting and routing of materials, businesses can accelerate throughput, minimize errors, and enhance order fulfillment accuracy. The key characteristic of automated sorting and routing is their ability to optimize material flow, reduce lead times, and enhance warehouse productivity. The unique feature of this automation lies in its capacity to integrate seamlessly with existing systems, offering enhanced operational flexibility, scalability, and efficiency.
IV. Safety Considerations in Conveyor Lift Systems
Ensuring safety is paramount in any industrial setting, especially concerning conveyor lift systems. Safety considerations are pivotal in maintaining a secure environment, safeguarding both equipment and personnel. By focusing on safety measures, companies can mitigate risks, prevent accidents, and adhere to industry regulations. Implementing robust safety protocols not only protects workers but also optimizes operational efficiency, reducing downtime due to mishaps.
A. Hazard Identification and Risk Mitigation
1. Safety Guard Installations
Safety guard installations play a critical role in preventing accidents and injuries within conveyor lift systems. These protective barriers help create a buffer between personnel and potential hazards, such as moving parts or high-temperature areas. The primary characteristic of safety guard installations is their ability to act as physical barriers, limiting access to dangerous machinery. Choosing to install safety guards is a prudent decision for any facility aiming to prioritize safety and adhere to safety standards.
2. Emergency Stop Protocols
Effective emergency stop protocols are crucial for swiftly halting conveyor lift systems in the event of an emergency. These protocols are designed to cease equipment operation immediately, reducing the risk of accidents or injuries. The key feature of emergency stop protocols is their ability to override automated processes and bring the system to a safe state promptly. While essential for safety compliance, emergency stop protocols may lead to temporary workflow interruptions. Balancing the need for rapid system halts with workflow continuity is key to optimizing safety in conveyor lift systems.
B. Operator Training and Awareness
1. Safety Guidelines for Personnel
Providing comprehensive safety guidelines for personnel is essential for cultivating a safety-conscious workforce. These guidelines educate employees on best practices, emergency procedures, and proper equipment usage. The key characteristic of safety guidelines is their emphasis on proactive safety measures, empowering employees to prevent accidents through informed decision-making. Incorporating safety guidelines not only enhances workplace safety but also fosters a culture of accountability and risk awareness.
2. Emergency Response Procedures
Efficient emergency response procedures are vital for addressing unforeseen events promptly and effectively. These protocols outline the steps to be taken in emergencies, ensuring a coordinated and efficient response from personnel. The unique feature of emergency response procedures is their structured approach, guiding employees through crisis situations systematically. While beneficial for minimizing damage and ensuring personnel safety, emergency response procedures require regular training and drills to maintain effectiveness. Investing in robust emergency response protocols is a proactive measure that enhances preparedness and minimizes downtime in critical situations.
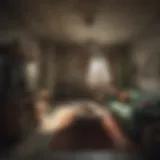
