Understanding Wooden Box Blueprints: A Guide
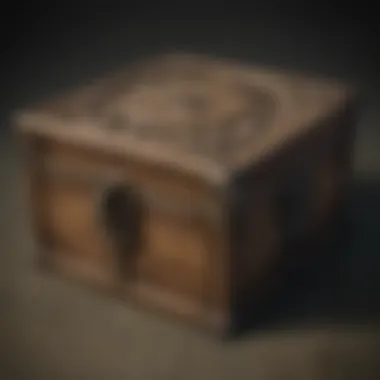
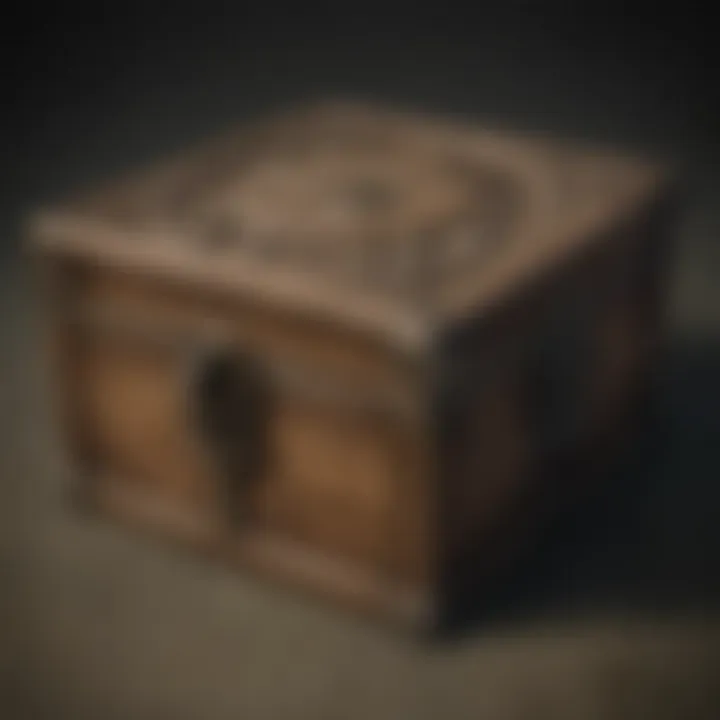
Intro
Woodworking and craftsmanship require more than just skills and tools; they rely heavily on plans and blueprints. In the context of wooden boxes, blueprints provide a visual representation of design, dimensions, and materials. This guide aims to explore wooden box blueprints in detail.
Recognizing the importance of blueprints is essential for any woodworker, whether they are just starting or have years of experience. Proper blueprints can save time, resources, and improve the overall quality of the final product. A well-crafted wooden box may serve various functions, from storage solutions to decorative pieces, making the understanding of design crucial.
This guide offers insights into the elements of drafting wooden box designs, exploring different styles, materials, and dimensions. We will take a closer look at common applications, tools, and techniques used in creating effective blueprints. The objective is to assist woodworkers in producing high-quality boxes by understanding blueprints and applying sound design principles.
The Importance of Wooden Box Blueprints
Wooden box blueprints serve as a critical component in woodworking and craftsmanship, acting as the roadmap for creating structures that are both functional and aesthetically pleasing. The design process begins with these blueprints, which allow woodworkers to visualize and plan their projects meticulously. A well-prepared blueprint reflects the dimensions, type of wood, joints, and finish, fundamentally determining the outcome of the project.
The significance of wooden box blueprints lies not only in the technical precision they afford but also in their ability to bridge creative ideas and practical execution. Such frameworks promote consistency across projects, ensuring each box meets specific requirements while maintaining design integrity. Moreover, blueprints facilitate communication among woodworkers, clients, and suppliers, minimizing misunderstandings during the crafting process.
Understanding the importance of wooden box blueprints also involves recognizing their historical context, which sheds light on the evolution of woodworking as a craft and as an industry.
Historical Context
The history of blueprints in woodworking can be traced back to ancient civilizations. Early artisans used rudimentary drawings to convey ideas. These drawings, often inscribed on tablets, were the precursors to modern blueprints. Over the centuries, blueprints evolved into more sophisticated methods, including detailed, scaled drawings that provide precise instructions for woodworking projects.
In the 19th century, the introduction of blueprints as we know them transformed the building and crafting industries. This technique allowed for duplication of designs, which directly contributed to the manufacturing of mass-produced items. The standardization offered by blueprints enabled skilled craftsmen to create furniture, storage solutions, and decorative pieces consistently and efficiently.
Today, the importance of wooden box blueprints remains evident. As craftsmanship often seeks to blend traditional methods with modern technology, these documents act as an anchor to historical woodworking practices while accommodating contemporary innovations.
Purpose and Utility
The purpose of wooden box blueprints extends beyond mere aesthetic appeal. They serve several practical functions that enhance both the design and construction processes. Firstly, blueprints allow for precision in measurements. A clearly defined plan minimizes the risk of costly errors that can occur from miscalculations or unclear designs.
Secondly, the utility of blueprints includes identifying the materials necessary for the project. Different types of wood offer various properties, such as strength, weight, and texture. A blueprint will specify the appropriate materials, ensuring durability and functionality.
Furthermore, blueprints can cater to specific applications. Whether the intended use is storage, decorative purposes, or functional tools, blueprints provide a tailored approach to design. They account for the box's intended purpose, supporting a thoughtful process that elevates the quality of the finished product.
Finally, blueprints facilitate efficient project management. By laying out a clear framework, woodworkers can organize their time and resources effectively, working towards a successful project outcome. This careful planning is essential for both amateur and experienced artisans, as it reinforces discipline, a core principle in any endeavor involving craftsmanship.
"A blueprint is not just a drawing; it is a vision translated to a structure that tells a story of design and functionality."
Key Components of a Wooden Box Blueprint
The key components of wooden box blueprints are essential for anyone undertaking woodworking projects. These elements contribute significantly to the craft, ensuring functionality and aesthetics align with the intended purposes. Properly understanding these components helps individuals achieve accuracy in design and execution. This is crucial whether one is a novice or an experienced woodworker.
Dimensions and Measurements
Dimensions and measurements form the backbone of any blueprint. They give exact values regarding the size of the box. Without precise measurements, the risk of creating a product that does not fit its intended use increases. Each dimension must be planned carefully. For example, the width, length, and height of a box must reflect the storage needs or the design aesthetic. Using a scale to represent these measurements allows for a clearer understanding of the final product. Measurements must be consistent throughout the blueprint to avoid confusion during the building process.
Materials Overview
Materials play a vital role in the quality and durability of wooden boxes. Thoughtful selection of wood types and finishes impacts both appearance and longevity. The components used in the box can either enhance or compromise its structural integrity.
Wood Types
When looking at wood types, one could consider options such as oak, pine, and maple. Oak is known for its strength and durability, making it a great choice for robust construction. Pine, on the other hand, is lighter and more affordable, appealing to budget-conscious projects. Maple provides an attractive finish due to its fine grain, perfect for decorative purposes. Each wood type has its unique characteristics, making them popular choices based on specific needs. While oak might resist wear well, it may also be heavier, which could be a disadvantage for projects needing portability.
Finishes and Treatments
Finishes and treatments are crucial in enhancing the final appearance of wooden boxes. They can protect the wood from moisture and wear. Using varnish can help to seal the wood, while treatments like stains can change the color without hiding the grain. Choices depend on the desired aesthetics and durability of the box. One might argue that applying oil treatments gives a natural feel, yet they may require more frequent reapplication compared to varnish. Therefore, understanding the pros and cons of each finish is essential for achieving the desired results.
Design Features
Design features add functional and visual appeal to wooden boxes. Incorporating elements like lids and hinges, handles and fasteners results in a well-rounded design.
Lids and Hinges
Lids keep the contents secure while providing easy access. Hinges must be chosen based on the size of the lid and the expected usage. For larger boxes, more robust hinges are necessary to support weight. A common option is the piano hinge, which runs along the full length of the box's lid. Its continuous support can be advantageous for larger designs. However, they require precise installation and space consideration. This is a key point for a blueprint.
Handles and Fasteners
Handles and fasteners are integral to a functional wooden box. Handles contribute to ease of transport, while having reliable fasteners ensures structural integrity. Types of handles can vary from recessed to pull-out styles, which affects both usability and aesthetic appeal. Fasteners, like screws, nails, or dowels, depend significantly on the type of wood used and the box's intended purpose. For instance, using dowels offers a clean finish, but may require more skill in execution compared to standard screws.
In summary, understanding these key components is significant for the effective execution of wooden box blueprints. Incorporating the right measurements, materials, and design features ensures that the final product meets both functional and aesthetic standards.
Common Styles of Wooden Box Designs
Understanding the various styles of wooden box designs is central to mastering the craft of woodworking. Different styles serve distinct purposes and offer unique aesthetic qualities, which can greatly influence the final product. Familiarity with these styles allows woodworkers to select the right design for specific uses, whether for storage, presentation, or functional applications. The beauty of wooden boxes lies not just in their functionality but also in their artistic expression. Each design conveys a sense of craftsmanship and intention.
Rectangular Boxes
Rectangular boxes are among the most common and versatile wooden box designs. Their straightforward shape allows for ample storage space, making them ideal for a variety of applications. They can be used for anything from organizing tools to serving as decorative elements in a home.
When drafting a blueprint for a rectangular box, it is important to consider the dimensions that best suit its intended use. This includes the height, width, and depth, which should align with the items to be stored. Additionally, rectangular boxes can be enhanced with features like lids that are either hinged or removable, adding functionality and style.
One significant benefit of rectangular boxes is their adaptability. They can be customized with different finishes and woods to match the environment they will reside in. Whether made of oak, pine, or mahogany, a rectangular box can be a statement piece in both rustic and modern settings.
Square Boxes
Square boxes offer a more compact option compared to rectangular ones. Their equal dimensions create a sense of symmetry, appealing to those who favor balanced aesthetics. These boxes are often used for smaller items, making them suitable for jewelry, keepsakes, or craft materials.
In designing a square box, it is essential to focus on detailed elements such as the corners and edges. These features can be emphasized through specific joinery techniques, impacting both the appearance and strength of the box. Moreover, the lid design should be carefully thought through, ensuring it meets both functional and aesthetic needs.
Square boxes can also be quite decorative. They provide a platform for intricate carvings or inlays, which can enhance their visual appeal. As with rectangular boxes, the choice of material can significantly affect the box’s final presentation and functionality.
Custom Shapes
Custom shapes pull woodworkers out of traditional design boundaries, allowing for unlimited creativity. These boxes can be tailored into various contours and sizes based on personal preference or the requirements of the items being stored. This flexibility opens avenues for unique gifts or special storage solutions.
The blueprinting process for custom shapes requires a thoughtful approach to measurements and design principles. It is essential to ensure that each angle and curve serves a purpose while maintaining structural integrity. Consideration must also be given to the balance between form and function, as some designs may be more challenging to execute than others.
"Custom shapes can encapsulate personal stories and individual designs, making them unique treasures."
Woodworkers often use advanced drafting software to create accurate representations of their ideas. This technological approach can simplify the design process for complex shapes, allowing for precise execution in the workshop.
Essential Tools for Drafting Blueprints
Drafting blueprints for wooden boxes is a meticulous process that requires precision and the right tools. The tools used can greatly influence the quality of the blueprints and ultimately, the final product. The importance of using appropriate tools cannot be overstated. They are essential in ensuring accuracy in measurements and clarity in designs. Understanding the tools available helps both new and experienced woodworkers create effective blueprints. The following sections will discuss specific categories of tools crucial for drafting, including measuring tools, drafting software, and drawing instruments.
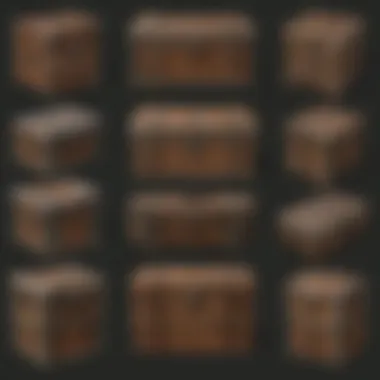
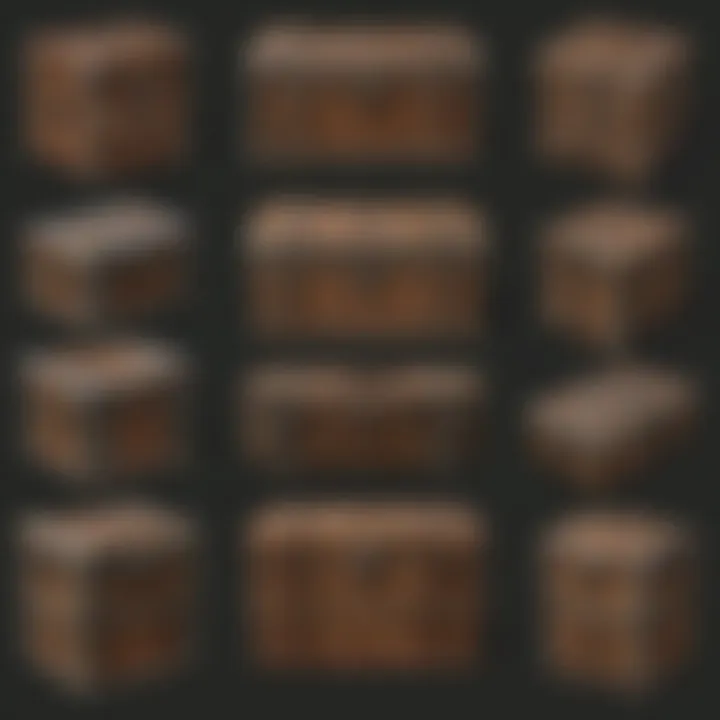
Measuring Tools
Tape Measures
Tape measures are foundational measuring tools in woodworking, including the drafting of blueprints. They offer a flexible, easy way to measure long distances accurately. A key characteristic of tape measures is their retractable design which allows for convenient storage without compromising on length. Tape measures are particularly beneficial for taking quick, linear measurements of larger pieces of wood, providing reliability in any project.
A unique feature of tape measures is their ability to hook on to the edge of materials, enabling users to measure from both ends of the tape. This can increase accuracy during the drafting process. However, the main disadvantage is that they may not be as precise for very detailed measurements, as they can be slightly less accurate than other tools.
Calipers
Calipers are another important tool for drafting blueprints, especially when precise measurements are required. They can measure the internal and external dimensions of objects, which is ideal for detailed wooden box design. A main characteristic of calipers is their capability to provide measurements in both metric and imperial units, making them versatile for various applications.
The unique feature of calipers is their ability to measure small dimensions accurately, such as the thickness of wood or the gap between assembled components. This specificity greatly enhances the overall accuracy of the blueprints. However, they can be more complex to use than tape measures, and improper handling may lead to measurement errors.
Drafting Software
Drafting software has transformed how woodworkers create blueprints. Programs can range from simple design applications to advanced CAD software. One significant advantage of using drafting software is the ability to produce precise, scale drawings efficiently. This digital approach allows for easy adjustments and modifications.
Software often includes built-in templates and libraries of standard dimensions, which can save time and reduce the chances of errors. Furthermore, they enable users to visualize the final product better through 3D modeling. However, a disadvantage may be that some users find digital tools less intuitive compared to traditional drafting methods. Learning curves can vary widely depending on the software's complexity.
Drawing Instruments
Pencils and Pens
Pencils and pens are fundamental instruments in the drafting process. Graphite pencils, in particular, are favored for their erasability and variety in tip hardness, which can create different line qualities. A key characteristic of using pencils is the ability to make adjustments on the fly without leaving permanent marks. This is essential when refining designs.
The adaptability of pencils is a significant advantage. However, they may not always provide the precision required for very fine details. Pens, especially technical drawing pens, offer sharper lines and are ideal for finalized designs. Yet, they limit the ability to modify previously drawn lines, which can lead to challenges.
Rulers and Squares
Rulers and squares are critical for ensuring straight lines and right angles in blueprints. Rulers serve as a reference point for maintaining accuracy across measurements. They are easy to use and increase efficiency when marking straight lines. A defining feature of rulers is their rigid body, which makes them reliable for drawing straight edges and measuring lengths accurately.
Squares, on the other hand, are crucial for ensuring that angles are accurate. They help in creating corners that are both functional and aesthetically pleasing in a wooden box design. While rulers are quite useful, squares may take more space and are limited to checking angles.
"Precision in drafting is not an option; it is a necessity for successful woodworking."
Blueprint Drafting Techniques
Drafting techniques are critical in the process of designing wooden boxes. This section focuses on the various methods used in creating blueprints that are not only functional but also ensure precision in the construction phase. Proper drafting techniques provide clarity in communication, reduce errors, and facilitate better planning for wooden box projects. Understanding these techniques is essential for both beginners and seasoned woodworkers, as they serve as the foundation for effective blueprint execution.
Sketching Initial Designs
The process of sketching initial designs is often the first step in drafting a blueprint for a wooden box. This technique allows the designer to quickly visualize ideas without being bound by precision measurements or complex software tools.
Sketching serves several important functions:
- Idea Generation: Freehand sketches encourage creativity. They allow woodworkers to explore various forms and concepts without the constraints of detailed technical drawings.
- Rough Proportions: Basic shapes and dimensions can be laid out. This initial sketch can help determine whether the design is practical and aesthetically pleasing before committing to a technical drawing.
- Communication Tool: A rough sketch can provide a basis for discussion with others. Sharing initial ideas with collaborators or clients can lead to feedback and further refinement.
To begin sketching, one should have simple materials, such as paper and pencils. Starting with basic geometric shapes, the sketched concept can grow into more complex designs as ideas develop.
Creating Technical Drawings
Once the initial sketch is developed, the next step is to create technical drawings. These drawings provide detailed specifications that are essential for building the wooden box. Unlike initial sketches, technical drawings demand accuracy and uniformity in measurements.
Key aspects of technical drawings include:
- Detailed Dimensions: Each part of the box needs clear dimensions, including length, width, and depth. This ensures that every component can be constructed to fit perfectly.
- Material Specifications: Identifying the type of wood and finishes plays a key role in the technical drawing. This information is critical for procurement and quality assurance.
- Construction Details: Technical drawings should outline the assembly methods and joint types used, including dovetail or finger joints. These details prevent misunderstandings during assembly.
To create a technical drawing, various tools can be employed:
- Drafting Software: Programs like AutoCAD or SketchUp can help produce precise and professional-looking drawings.
- Manual Drafting Tools: For those who prefer traditional methods, rulers, compasses, and drafting tables are still valuable tools.
"Well-drafted technical drawings are the bridge between an idea and its realization in wood. They transform conceptual sketches into actionable plans."
In summary, mastering blueprint drafting techniques is foundational to successful woodworking projects. From the initial phases of sketching to the refinement of technical drawings, each step plays a vital role in ensuring that the final product meets the expectations both in aesthetics and function.
Working with Dimensions and Scale
Working with dimensions and scale is essential when drafting wooden box blueprints. Accurate measurements form the foundation of any woodworking project. Discrepancies in dimensions can lead not only to aesthetic issues, but also to structural problems. Hence, understanding scale drawings and conversion factors is vital for both novice and skilled woodworkers.
Understanding Scale Drawings
Scale drawings provide a simplified representation of the actual size of the project. They allow woodworkers to visualize the final product and determine how components fit together before actual construction begins. In practice, a scale drawing is a down-sized or up-sized version of the object, maintaining the same proportions.
For example, a wooden box might be planned in a 1:2 scale. This means that every 1 unit on the drawing equals 2 units in the real world. Scale drawings are particularly useful for fitting intricate designs within limited spaces. It also aids in identifying how many materials will be needed and how they can be arranged.
When creating scale drawings, it’s important to select an appropriate scale. The choice will depend on the size of the project and the detail needed. A larger scale may provide more detailed information; however, it could make the drawing cumbersome. Thus, a balance between clarity and practicality must be achieved.
Conversion Factors
Conversion factors are equally important in blueprint creation, particularly when dealing with measurements in different units. Woodworkers often encounter dimensions expressed in inches, feet, centimeters, or millimeters. Knowing how to convert these measurements accurately ensures a consistent approach when drafting blueprints.
To convert from one unit to another, specific multiplication or division factors are applied. For instance:
- To convert inches to centimeters, multiply the number of inches by 2.54.
- To convert feet to inches, multiply the number of feet by 12.
Using the right conversion factors reduces the chances of errors in measurements and ensures consistent results throughout the woodworking process. This is particularly vital when multiple people are involved in the project, as misunderstandings can quickly lead to significant issues.
Remember: Always double-check conversions and calculations; small errors can have large repercussions.
Implementing Design Principles
Implementing design principles is a critical aspect of creating wooden box blueprints. This section discusses various design elements that can affect the performance and aesthetic of a wooden box. Proper design principles lead to better efficiency, usability, and overall satisfaction in the product.
Balance and Proportion
Balance in design refers to the visual stability of a wooden box. It is about ensuring that the weight and size of components are harmoniously distributed. A well-balanced box does not feel heavy on one side. For example, if a box is larger, it may need wider handles to maintain balance. Proportion deals with the relationship between the dimensions of the box and its parts. The size of the lid compared to the body, or the thickness of the walls, should be visually appealing and functionally sound. Maintaining balance and proportion can lead to a more enjoyable user experience as well as increased structural integrity.
- Key Considerations:
- Benefits:
- Maintain equal weight distribution.
- Ensure lid size is proportional to body size.
- Use thicker materials for larger boxes to enhance stability.
- Enhanced visual appeal
- Improved functionality
- Increased structural longevity
Functional Design Considerations
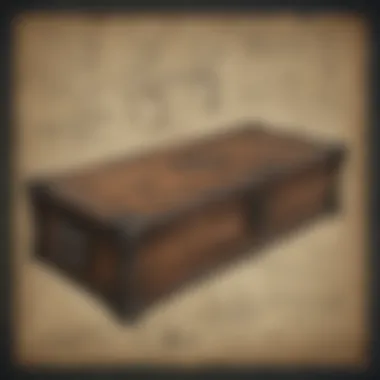
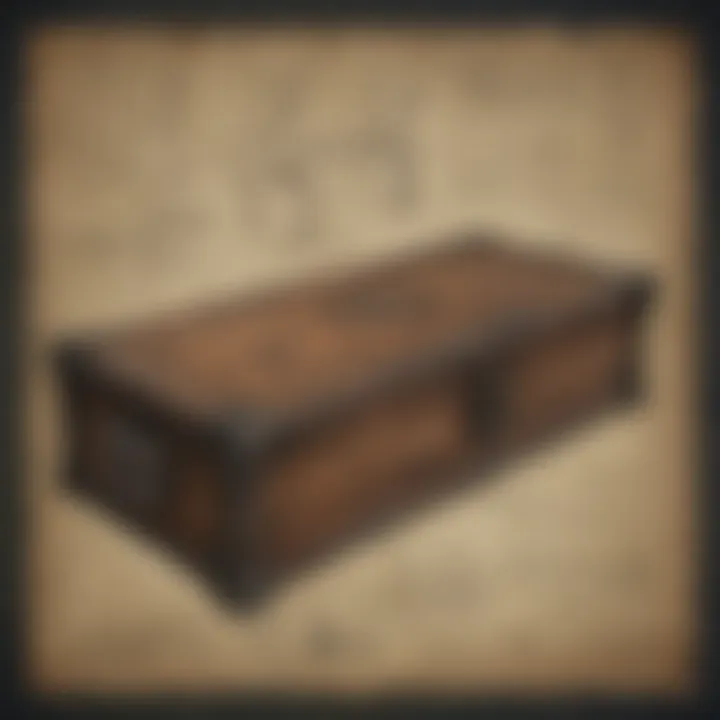
Functional design is all about practicality. Each element in the design must serve a purpose, whether it is decorative or structural. For wooden boxes, this means addressing how they will be used. Understanding the intended application is crucial. A box for storage has different requirements than a display box.
Important factors include:
- Accessibility: Consider how easily the box can be opened and closed.
- Durability: Choose materials and construction techniques that can withstand the expected use.
- Modularity: Designing for easy disassembly can add functional flexibility.
Moreover, ensuring that design principles prioritize both aesthetics and usability can significantly enhance user experience. Repeatedly following these principles leads to better outcomes and projects that meet expectations effectively and practically.
Applications of Wooden Boxes
The applications of wooden boxes extend well beyond mere storage. They play a significant role in various domains, ranging from functional use to aesthetic appeal. Understanding these applications helps woodworkers and enthusiasts appreciate the versatility and practicality of wooden box designs. Each application not only highlights the utility of wooden boxes but also showcases the artistry that goes into their construction.
Storage Solutions
Wooden boxes serve as a prominent solution for storage needs. Their sturdy construction allows them to keep items safe from damage and dust. Whether used for household storage, workshop organization, or outdoor tools, wooden boxes excel in functionality. The ability to customize dimensions and features makes them suitable for various purposes, like:
- Seasonal Item Storage: Wooden boxes are excellent for keeping holiday decorations and seasonal clothing safe.
- Craft Supplies: Organizing tools and materials becomes easier with appropriately sized boxes.
- Toys and Games: Children’s toys can be neatly stored, reducing clutter in living spaces.
In addition to practicality, wooden boxes add a touch of natural elegance to any storage solution. The warmth of wood enhances a room's aesthetic while providing a rugged durability. This combination of function and form makes wooden boxes an ideal choice for many storage applications.
Decorative Purposes
The decorative potential of wooden boxes is vast. They can act as statement pieces in an interior design scheme or serve subtle roles in enhancing the overall ambiance. Various factors influence their decorative use, including:
- Finishes and Stains: A well-finished wooden box can showcase its natural grain and beauty.
- Distinctive Designs: Unique carvings or patterns can make a box a focal point in a room.
- Personalization: Customization options, such as monograms or themed designs, allow for personal expression.
Wooden boxes can also function beautifully as decorative organizers on tables or shelves. Using smaller boxes within larger arrangements creates depth and interest. Their versatility makes them suitable for various styles, including rustic, modern, or traditional.
Functional Tools
Beyond decoration and storage, wooden boxes serve practical purposes, working as functional tools in various settings. Here are some examples:
- Toolboxes: Many woodworkers use custom wooden boxes to store and transport their tools effectively.
- Workshop Organizers: Specific boxes can be designed to suit various tools and materials, optimizing workspace efficiency.
- Planters: Wooden boxes can be repurposed as planters, enhancing gardens while also functioning to hold soil and plants.
In summary, the applications of wooden boxes are numerous, meeting various needs in storage, decoration, and functionality. Understanding these diverse uses helps both creators and users appreciate the multifaceted nature of wooden boxes. Their ability to combine function and artistry ensures they remain relevant tools across different contexts.
Ensuring Structural Integrity
Ensuring structural integrity is a fundamental aspect of working with wooden box blueprints. It directly affects the durability and function of the final product. Any miscalculation or oversight in this area can lead to structural failures, such as collapse or deformation, which can compromise both the utility and aesthetic value of the wooden box.
When drafting designs, it is essential to consider how different elements such as joint types and load-bearing capabilities come together. These factors not only influence the craftsmanship but also impact how the box will perform in practical use.
Joint Types and Their Applications
Understanding different joint types is crucial for maintaining structural integrity. Each joint has specific applications and strengths, which can enhance the strength or flexibility of the design. Common joint types include:
- Butt Joint: This is the simplest joint, where two pieces meet at their ends. While easy to make, it is less strong unless reinforced.
- Dovetail Joint: Known for its resistance to pulling apart, this joint is often used in drawer construction. Its interlocking tails create a strong bond.
- Mortise and Tenon Joint: This traditional joint connects two pieces at right angles, providing excellent support and strength.
Selecting the appropriate joint for the wooden box is essential. Each joint's performance can vary based on the materials and design constraints, which makes understanding these differences vital for a successful build.
Load-Bearing Considerations
Load-bearing considerations are another critical component when ensuring structural integrity. The design must account for the various forces applied to the wooden box during use. Factors to consider include:
- Weight Capacity: Knowing how much weight the box needs to support will inform decisions on materials and dimensions.
- Material Selection: Different wood types have varying strength characteristics. Hardwoods like oak and maple generally offer better load-bearing capabilities than softwoods like pine.
- Distribution of Weight: An evenly distributed weight reduces stress on joints and materials, while concentrated loads can lead to failures.
Proper calculations regarding load-bearing will ultimately determine the longevity and functionality of the wooden box. Understanding these principles helps achieve a solid design that stands the test of time.
"The choice of joints and load-bearing materials is not just about aesthetics; it is about the life and endurance of the wooden box itself."
Finishing Touches
In woodworking, finishing touches are critical for enhancing both the aesthetic appeal and durability of wooden boxes. The final steps taken in the finishing process can determine the overall look and functionality of the box. It is during this phase that woodworkers ensure that the piece not only fulfills its intended purpose but also exemplifies quality craftsmanship.
Sanding Techniques
Sanding is a foundational aspect of the finishing process. Proper sanding smooths out rough edges and prepares the wood for additional treatments. The grit of sandpaper plays a vital role here: starting with coarser grits for initial smoothing and progressing to finer grits for a polished finish.
- Initial Sanding: Use 80-grit sandpaper to reshape and remove any imperfections. This might include marks from saw blades or other tools used during construction.
- Intermediate Sanding: Progress to 120-grit paper. This step smoothens the surface further and prepares it for finer grits.
- Final Sanding: A final pass with 220-grit sandpaper offers a soft finish that is ready for staining or varnishing.
Each pass should be done along the grain of the wood to avoid scratches that can detract from the final appearance. Sanding not only improves the look but also helps the chosen finish adhere better.
Application of Finishes
The application of finishes is essential for protecting wooden boxes from wear and enhancing their visual characteristics. Two popular finishes used in this process are varnish and stain, each serving distinct purposes and offering unique benefits.
Varnish
Varnish is a clear, hard finish that provides excellent protection against moisture and abrasion. Its key characteristic is the ability to enhance the natural beauty of the wood while forming a durable barrier on the surface. Varnish is frequently considered a beneficial choice because it:
- Preserves Wood: It helps prevent damage from water and UV rays.
- Provides a Glossy Finish: This enhances the wood grain and color deeply.
A unique feature of varnish is its ability to be applied in multiple coats. Each coat increases the depth of the finish, producing a rich, glossy effect. However, the drying time can be longer, and it requires a well-ventilated area for application.
Stain
Stain serves a different purpose; it adds color to the wood while allowing the grain to show through. Its key characteristic is its ability to penetrate deeply into the wood fibers, providing a vibrant hue. Stain is a popular choice for various reasons:
- Variety of Colors: Stains come in many colors, enabling customization.
- Ease of Application: Stains can often be applied with a brush or cloth and require less drying time than varnish.
One unique feature of stain is its ability to highlight the natural imperfections in the wood, which some woodworkers find appealing. However, it does not provide as robust a layer of protection as varnish, and a top coat may be necessary for enhanced durability.
Ultimately, the choice between varnish and stain—or even a combination of both—depends on the desired finish and the function of the wooden box. Both techniques contribute significantly to the overall success of the project.
Common Challenges in Blueprint Execution
Executing wooden box blueprints successfully is not simply about following a set of drawings. It requires critical attention to detail at every phase of the construction process. Missteps can lead to wasted materials, incorrect dimensions, or poorly designed boxes that do not meet intended uses. By understanding common challenges, woodworkers can enhance their skills and improve the outcomes of their projects. This section emphasizes the importance of recognizing potential issues and explores ways to address them effectively.
Identifying Errors in Measurements
Accurate measurements are the foundation of any woodworking project. Errors can occur from miscalculating dimensions, using the wrong tools, or even human error in reading the scale. For example, if a box's length is off by even a small fraction of an inch, it can lead to components that do not fit together properly.
- Common Sources of Error:
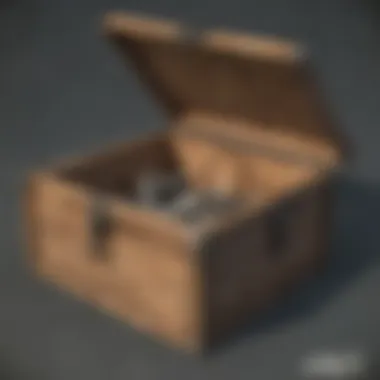
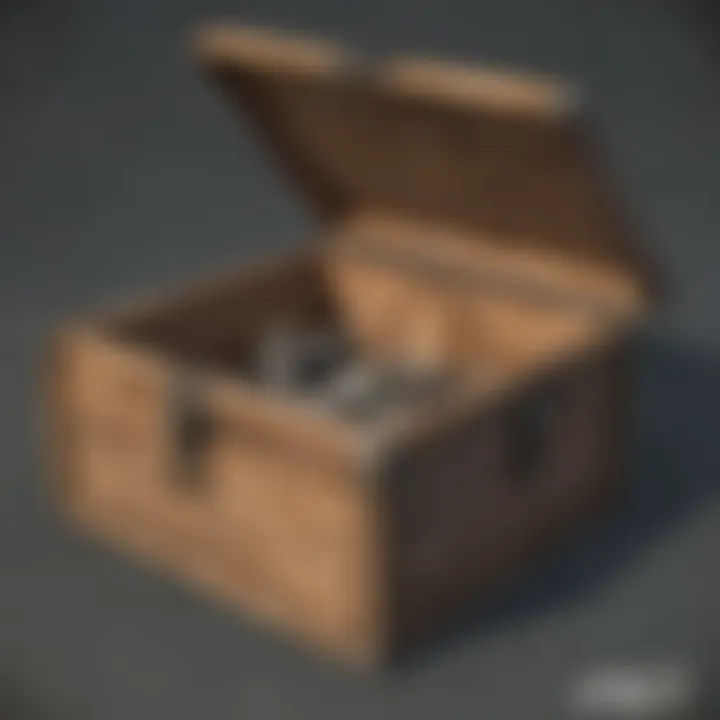
- Not double-checking measurements before cutting.
- Using inappropriate measuring tools.
- Failing to account for the thickness of materials.
Identifying these errors early on is crucial. A careful review of each measurement before beginning the execution phase can save time and frustration. Additionally, if measurements are consistently incorrect, it’s worth evaluating measuring techniques and tools. Constant vigilance ensures that craftspeople work with precision.
Troubleshooting Design Flaws
Despite meticulous planning and execution, design flaws can still emerge during assembly. These issues may arise from the blueprint itself or from unexpected challenges during the construction phase. Craftspersons may find that parts do not align as intended, storage options are inadequate, or aesthetic choices do not complement the intended design.
A few steps to troubleshoot design flaws include:
- Reviewing the Blueprint: Go over the initial plans to ensure all aspects are accounted for. Look for instructions that may have been misunderstood.
- Mock-Up Construction: Sometimes, creating a rough version of the box can help visualize how all parts fit together before using final materials.
- Gather Feedback: Seeking input from peers or expert woodworkers can provide another perspective on design issues that may not be immediately evident.
Ultimately, embracing the challenge of troubleshooting leads to enhanced design skills and a greater understanding of wooden box construction. Recognizing when a project needs adjustments can be critical to producing high-quality work.
"In woodworking, precision is not simply an option; it is the essence of craft."
By addressing challenges related to measurements and design flaws, woodworkers can improve their overall craftsmanship and create wooden boxes that meet both functional and aesthetic needs.
Evaluating Finished Projects
Evaluating finished projects is a crucial step in the woodworking process. The evaluation ensures that the craftsmanship meets the initial design intentions. It involves examining various aspects, such as structural integrity, aesthetic appeal, and functional performance. By focusing on evaluation, woodworkers can identify areas for improvement in future designs and enhance their skills.
Quality Control Standards
Quality control standards are essential in assessing wooden box projects. These standards provide benchmarks that help determine if a project meets the desired specifications. Common quality control elements include:
- Measurement Accuracy: Checking that dimensions align with the blueprint ensures that every piece fits properly.
- Joint Integrity: Evaluating the strength and durability of joints is critical for long-term use.
- Surface Finish: The final look of the box should meet basic aesthetic criteria.
By adhering to these standards, woodworkers can elevate the quality of their projects, ensuring consistency and reliability.
Post-Completion Assessments
Post-completion assessments serve as the final evaluation of a wooden box project. This assessment focuses on practical aspects and overall satisfaction. Key elements to consider include:
- Functionality Check: Ensuring that the box performs its intended purpose without issues.
- Durability Analysis: Assessing how well the box stands up to expected wear over time.
- User Feedback: Gathering insights from anyone who interacts with the box can reveal unforeseen issues or strengths.
"Evaluating finished projects allows woodworkers to acknowledge their successes while learning from their mistakes."
In summary, evaluating finished projects not only highlights craftsmanship but also provides valuable lessons for future work. It encourages a continuous improvement mindset, which is vital in woodworking.
Resources for Further Study
In the realm of woodworking, the quest for knowledge is incessant. For those engaging with wooden box blueprints, understanding can take various forms. Resources for further study serve to enrich this journey, offering a blend of theory and practical insights.
Benefits of utilizing these resources are manifold. First, they provide a foundation on which to build advanced skills. Readers can explore diverse techniques, acknowledge critical design principles, and gain insight into material properties. Manuals often explain complex concepts in a straightforward manner. This fosters clarity and depth of understanding.
Additionally, staying informed about current trends can influence design choices. The woodworking landscape is ever-evolving. Resources allow woodworkers to grasp innovations, ensuring that their projects remain relevant. Engaging with updated materials ensures that one does not adhere to outdated methodologies.
When considering resources, evaluate the depth of content. A well-structured book or manual can be invaluable for beginners. However, seasoned professionals may prefer nuanced discussions found in specialized forums and communities. The combination of both can offer a holistic view of the craft.
"Continuous learning transforms a skilled woodworker into a master artisan."
Moreover, utilizing diverse resources enhances problem-solving abilities. Many books offer case studies, which illustrate how others approached specific challenges. This can inspire unique solutions or inventive modifications. When one encounters a particular design hurdle, searching through forums can also prompt new ideas from fellow woodworkers.
In summary, resources for further study are essential for anyone serious about mastering wooden box designs. They not only broaden knowledge but also stimulate innovation. As one delves deeper into the craft, the integration of various materials will surely elevate the quality and creativity of future projects.
Books and Manuals
Books and manuals are great starting points for anyone interested in wooden box blueprints. They provide foundational knowledge and often include examples that illustrate concepts effectively. This format allows learners to visualize how theory translates into practice.
When selecting books, consider:
- Comprehensiveness: Look for texts that cover a broad range of techniques and designs.
- Author Expertise: Choose manuals written by established woodworkers or educators in the field.
- Visual Aids: Diagrams and photographs enhance understanding, especially for complex blueprints.
Books like The Complete Manual of Woodworking offer a well-rounded perspective, addressing everything from basic design principles to detailed construction techniques. These resources serve as reliable guides.
Online Forums and Communities
Engaging with online forums and communities can greatly supplement traditional study. Platforms such as Reddit and specialized woodworking sites foster discussions among enthusiasts and professionals. Here, individuals share experiences, troubleshooting tips, and innovative designs.
Benefits of participating include:
- Real-Time Problem Solving: Post questions or challenges and receive feedback promptly.
- Access to Diverse Perspectives: Members from various backgrounds offer unique insights, enhancing learning.
- Networking Opportunities: Building connections can lead to mentorship or collaborative projects.
Join forums dedicated to specific interests, such as box-making or restoration techniques. Facebook groups also provide spaces for discussion and sharing work, making it easier to find community support.
Ultimately, both books and online communities play critical roles in advancing one's understanding of wooden box blueprints, helping enthusiasts grow into skilled crafters.
The Future of Wooden Box Design
The exploration of The Future of Wooden Box Design showcases the evolving landscape of craftsmanship and creativity within woodworking. As technology permeates traditional practices, fresh opportunities emerge for designers and artisans. This section underscores the relevance of staying abreast with advancements, ensuring that wooden box designs do not merely adapt but thrive in contemporary settings.
In today's marketplace, the integration of cutting-edge materials and innovative technologies transforms how wooden boxes are conceived and executed. This evolution emphasizes efficiency, sustainability, and aesthetic appeal, paving the way for a new breed of woodworkers who challenge the status quo. Ensuring a future-ready approach is essential not just for environmental considerations, but also for meeting diverse consumer demands that prioritize both functionality and design.
Trends in Material Usage
The movement towards sustainable practices influences the trends in material usage for wooden box designs. Many woodworkers opt for reclaimed wood and bamboo, as these materials offer durability alongside environmental responsibility. Reclaimed wood, with its unique character, contributes to the aesthetic qualities of boxes, while bamboo provides a lightweight yet solid alternative.
Additionally, advancements in composite materials have caught the attention of designers. These materials blend traditional wooden elements with modern synthetics. This allows the creation of boxes that can withstand harsher elements and provide better structural integrity. Such innovations are not just about performance; they also reflect a shift in consumer values toward eco-friendliness and sustainability.
- Natural materials currently trending include:
- Composite options gaining popularity:
- Reclaimed wood
- Bamboo
- Plywood laminated with sustainable finishes
- Wood-plastic composites
- Engineered woods
This focus on materials not only drives the design but also enhances marketability, as consumers increasingly seek products that tell a story and contribute positively to their lifestyles.
Innovations in Design Technology
The influence of digital technology on the design and crafting of wooden boxes cannot be overstated. CAD software has revolutionized how blueprints are created, allowing for intricate designs that were previously challenging to render. These technologies support precision, enabling woodworkers to design components with exact specifications.
Moreover, 3D printing is emerging as a companion tool in the woodworking realm. While it primarily excels in producing prototypes, the integration of 3D printing with traditional woodworking opens avenues for customized designs. Artisans can create detailed components which can then be incorporated into wooden box projects, enhancing creativity and uniqueness.
Moreover, on-demand manufacturing platforms are reshaping the availability of designs. Woodworkers can now share and monetize their blueprints with a broader audience. This democratization of design fosters innovation and encourages a collaborative spirit among creators.
New technologies offer not only enhanced functionality but also an opportunity for artisans to make their mark in a saturated market. By embracing these innovations, craftsmen can redefine what wooden boxes can be, ensuring their relevance in the years to come.
"The evolution of technology not only improves the process of creation but also enhances the final product, making it indispensable in modern woodworking."
In summary, the future of wooden box design is marked by a commitment to sustainability, a shift towards innovative materials, and the integration of advanced technologies. As these trends continue to develop, they will shape the practices of current and future woodworkers, leading to a promising horizon in the crafting of wooden boxes.